Case
what is in a cement production factory
2023-12-13T18:12:02+00:00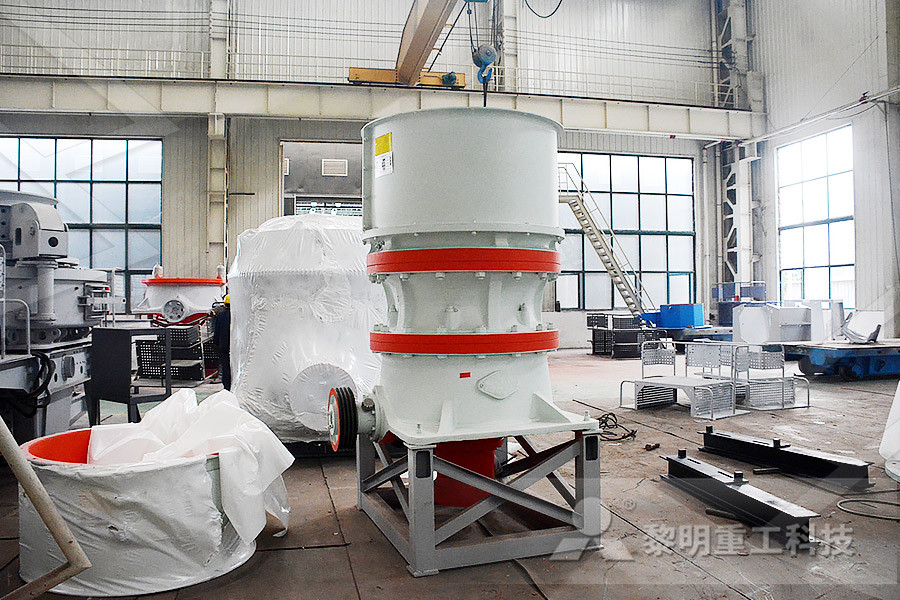
Cement Production an overview ScienceDirect Topics
Cement production is a thermal energy intensive process, which requires heating solid particles up to 1450°C and cooling it down The process generates hot and CO2 rich exhaust streams92 Cement Industry In the cement industry, coal quality is very important as it affects both the quality of the cement and the operation of the plant The Indian cement industry uses coal because of its abundant availability and shortage of oil and natural gas Today the Indian cement industry has to use coal of high ash content with varying Cement Industry an overview ScienceDirect TopicsThe main materials used in cement production are minerals containing calcium oxide, silex, alumina and iron oxide These components are rarely found in one type of raw material; therefore, for the cement production the raw mix is selected for the following components:RAW MATERIALS IN CEMENT PRODUCTIONFeb 24, 2021 The cement manufacturing process is completed when the cooled clinker is ground once again in a rotating finishing mill A combination of gypsum and limestone will usually be added in small amounts to the heated cement during this last grinding step, and coloring agents can also be added here The fineness of the finished particles will vary according to individual preferences, and the cement What Is the Cement Manufacturing Process? (with pictures)Cement is manufactured through a closely controlled chemical combination of calcium, silicon, aluminum, iron and other ingredients Common materials used to manufacture cement include limestone, shells, and chalk or marl combined with shale, How Cement Is Made Portland Cement Association
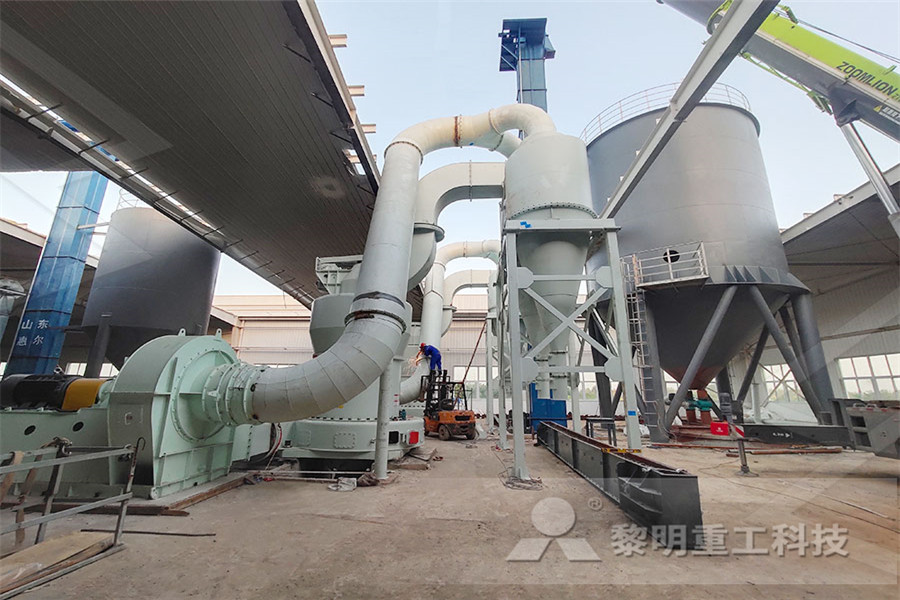
Cement Manufacturing Process Phases Flow Chart
Aug 30, 2012 Cement Manufacturing Process Phase 1: Raw Material Extraction Cement uses raw materials that cover calcium, silicon, iron and aluminum Such raw materials are limestone, clay and sand Limestone is for calciumA concrete plant, also known as a batch plant or batching plant or a concrete batching plant, is equipment that combines various ingredients to form concrete Some of these inputs include water, air, admixtures, sand, aggregate (rocks, gravel, etc), fly ash, silica fume, slag, and cement A concrete plant can have a variety of parts and accessories, including: mixers (either tilt drum or horizontal or in some cases both), cement batchers, aggregate batchers, conveyors, radial stackers, aggregate bins, cement bins, heatersConcrete plant WikipediaIn a cement production plant, limestone and other raw materials such as silicate, bauxite, iron ore, etc are heated so that molecules of carbon dioxide are liberated from the limestone to form quicklime, which combines with the other ingredients, resulting in the formation of calcium silicates and other productsWhat is Cement? History Chemistry Industries Civil The cement manufacturing industry was an EPA New Source Review/Prevention of Significant Deterioration (NSR/PSD) national enforcement initiative in fiscal years 20082010 and was continued as a Reducing Air Pollution from the Largest Sources national enforcement initiative for fiscal years 20112013 The cement sector is the third largest industrial source of pollution, emitting more than Cement Manufacturing Enforcement Initiative US EPAAshoka's cement plant unit has continued focused on objectives of product improvement and quality In our entire turnkey cement plant equipments and machinery, we supply a complete assembly consisting of different machines and equipment, which facilitate the plant to execute efficiently and manufacture a betterquality completed product as per the international quality standardscement plant equipments manufacturer and suppliers of
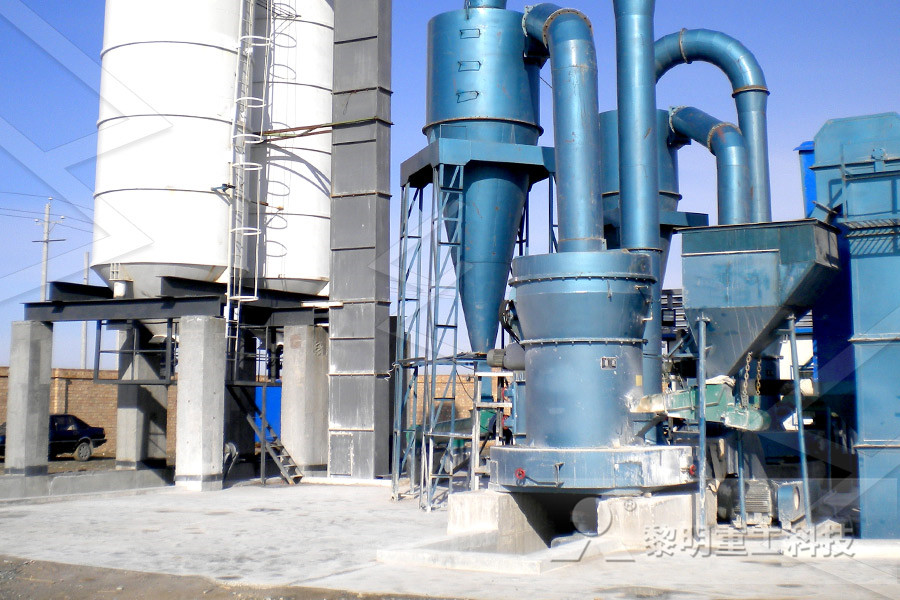
The Cement Manufacturing Process Advancing Mining
Domestic cement production has been increasing steadily, from 664 million tons in 2010 to about 805 million tons of Portland cement in 2014 according to the US Geological Survey 2015 Cement Mineral Commodity Summary The overall value of sales of cement Feb 24, 2021 The cement manufacturing process is completed when the cooled clinker is ground once again in a rotating finishing mill A combination of gypsum and limestone will usually be added in small amounts to the heated cement during this last grinding step, and coloring agents can also be added here The fineness of the finished particles will vary according to individual preferences, and the cement What Is the Cement Manufacturing Process? (with pictures)The industry includes about 190 cement manufacturing establishments, about 5,700 readymix concrete manufacturing establishments, and about 900 establishments that make concrete block, brick, pipe, and other concrete products COMPETITIVE LANDSCAPE Demand is determined primarily by nonresidential and residential construction activityCement Concrete Product Manufacturing Industry Profile A concrete plant, also known as a batch plant or batching plant or a concrete batching plant, is equipment that combines various ingredients to form concreteSome of these inputs include water, air, admixtures, sand, aggregate (rocks, gravel, etc), fly ash, silica fume, slag, and cementA concrete plant can have a variety of parts and accessories, including: mixers (either tilt drum or Concrete plant WikipediaCement production per capita has increased considerably (see Table 2) Based on this index, the USSR has led such developed countries as the USA (330 kg) and Great Britain (285 kg) since 1966 The raw material base for the cement industry is the calcareous and argillaceous rock widely found in Cement Industry Article about Cement Industry by The
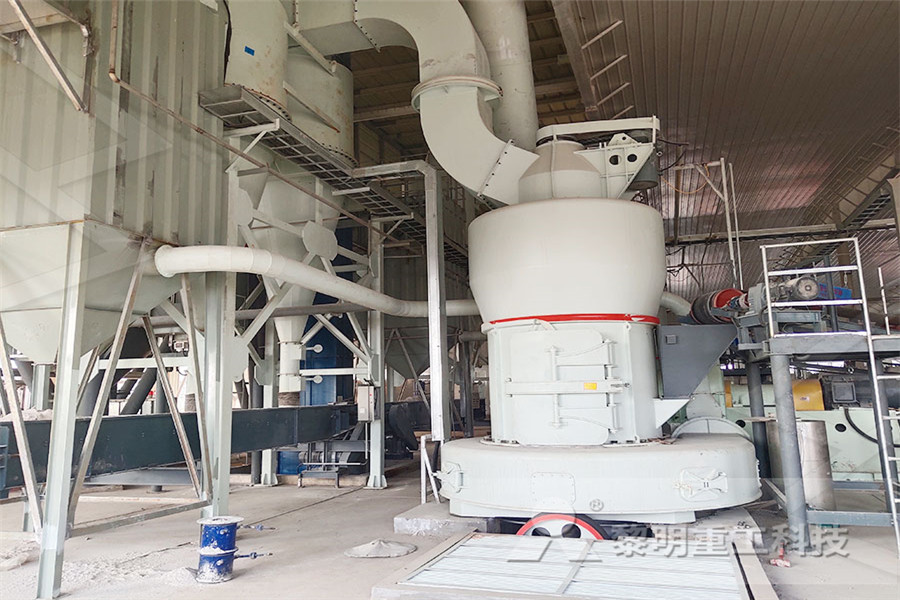
Cement Manufacturing Enforcement Initiative US EPA
The cement manufacturing industry was an EPA New Source Review/Prevention of Significant Deterioration (NSR/PSD) national enforcement initiative in fiscal years 20082010 and was continued as a Reducing Air Pollution from the Largest Sources national enforcement initiative for fiscal years 20112013 The cement sector is the third largest industrial source of pollution, emitting more than Jul 31, 2013 Follow us: https://instagram/7activestudio/For more information:7activestudio7activestudio@gmailContact: +91 , 040Cement Manufacturing YouTubeThe Global Cement Market production capacity stood at 522 billion tons in 2018 And is expected to register a CAGR of 62% during the forecast period from 2019 to 2025, Cement is a binding agent used for joining or hold of different materials, usually fine powders of inorganic materials with key constituents as limestones, calcium silicate, chalk, shells, and othersCement Market Size, Share, Trends and Industry Forecast to What’s involved with starting a cement business? Determine the type of cement you want or can produce and the raw materials available in your region Is it necessary to import raw materials? Common materials include limestone, shells and chalk, clHow much does it cost to set up a cement factory? QuoraAshoka's cement plant unit has continued focused on objectives of product improvement and quality In our entire turnkey cement plant equipments and machinery, we supply a complete assembly consisting of different machines and equipment, which facilitate the plant to execute efficiently and manufacture a betterquality completed product as per the international quality standardscement plant equipments manufacturer and suppliers of
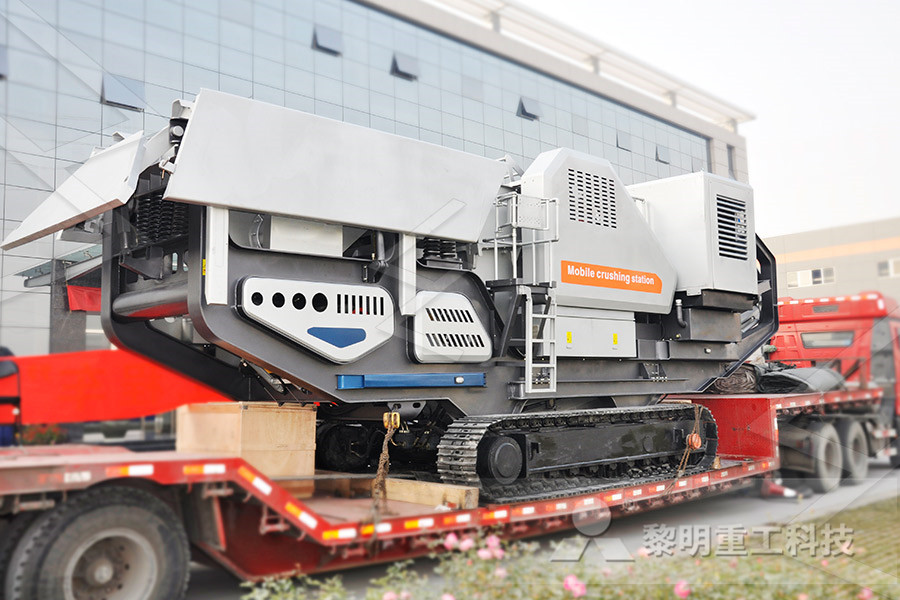
cement plant cost Page 1 of 2
May 01, 2010 cement plant cost what is the cost of a new cement plant of 2 MTPA? what is the cost of erection for the same cost of iron for the same? rajesh Reply Know the answer to this question? Join the community and register for a free guest account to post a replyStage of Cement Manufacture There are six main stages of cement manufacturing process Stage 1 Raw Material Extraction/Quarry The raw cement ingredients needed for cement production are limestone (calcium), sand and clay (silicon, aluminum, iron), shale, fly ash, mill scale and bauxite The ore rocks are quarried and crushed to smaller pieces of about 6 inchesCement Manufacturing Process Civil EngineeringCement Production: Raw Meal Production in Steps Perfectly mixed, accurately fed without pulsation, and precisely weighed The key word is quality! And this quality is achieved during cement production with exactly matched process steps In the first stage, the raw meal is produced, as described belowCement Production: Raw Meal Production in StepsAt the cement production factory, the proportions of the various raw materials that go into cement must be checked to achieve a consistent kiln feed, and samples of the mix are frequently examined using Xray fluorescence analysis The strength of concrete is probably the most important property that must be tested to comply with specificationsHow concrete is made material, manufacture, making, how Stage of Cement Manufacture There are six main stages of cement manufacturing process Stage 1 Raw Material Extraction/Quarry The raw cement ingredients needed for cement production are limestone (calcium), sand and clay (silicon, aluminum, iron), shale, fly ash, mill scale and bauxite The ore rocks are quarried and crushed to smaller pieces of about 6 inchesCement Manufacturing Process Civil Engineering
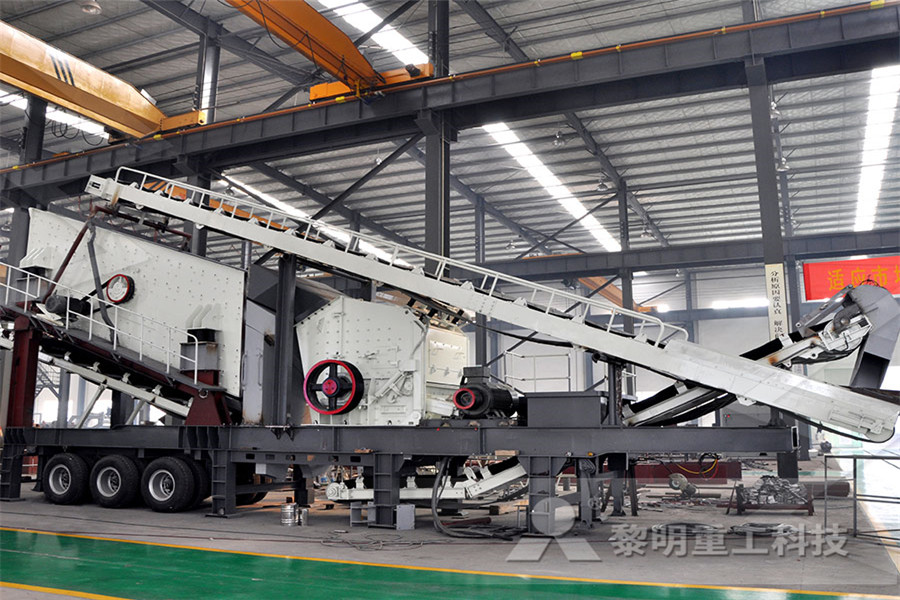
What Is the Cement Manufacturing Process? (with pictures)
Feb 24, 2021 The cement manufacturing process is completed when the cooled clinker is ground once again in a rotating finishing mill A combination of gypsum and limestone will usually be added in small amounts to the heated cement during this last grinding step, and coloring agents can also be added here The fineness of the finished particles will vary according to individual preferences, and the cement Oct 22, 2015 When this paste is mixed with sand and gravel and allowed to dry it is called concrete 3 Limestone Quarry and Crushing Plant The major raw material for cement production is limestoneThe limestone most suitable for cement production must have some ingredients in specified quantities ie, calcium carbonates, silica, alumina, iron, etcCement Plant Process and Instruments UsedHi, Following three distinct operations are involved in the manufacturing of normal setting or Portland ordinary cement: 1 Mixing of raw materials 2 Burning 3 Grinding MIXING OF RAW MATERIALS The raw materials such as limestone or chalk and shaWhat is the manufacturing process of cement? QuoraThe global cement market reached a volume of 491 Billion Tons in 2020 Cement refers to a binding material widely used for construction purposes that is manufactured by grinding a Cement Market Share, Size, Industry Analysis Report Cement production also is a key source of CO2 emissions, due in part to the significant reliance on coal and petroleum coke to fuel the kilns for clinker production Globally, CO2 emissions from cement production were estimated at 829 MMTCO2 in 2000 7, approximately 34% of global CO 2 emissions from fossil fuel combustion and cement productionCO2 Emissions Profile of the US Cement Industry
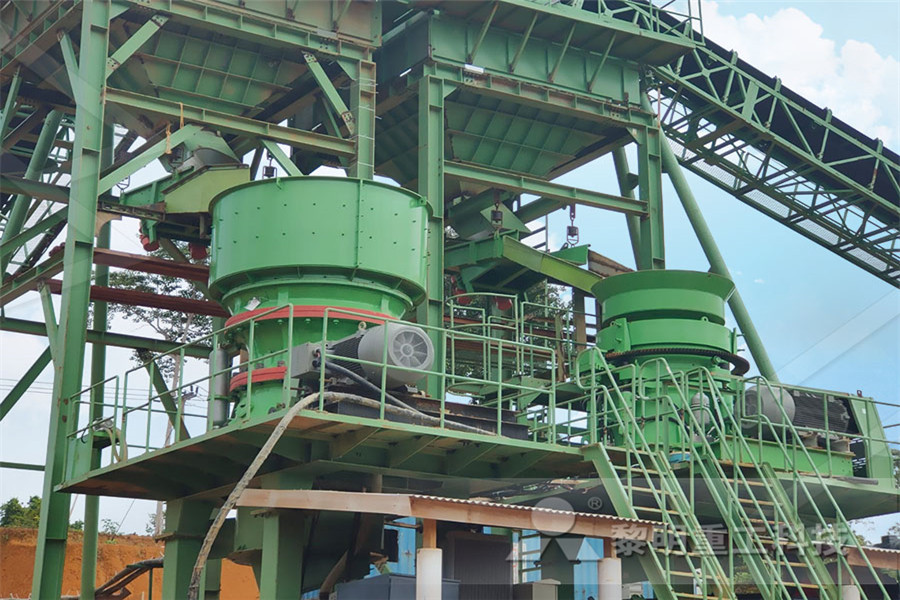
Lehigh Cement Company Lehigh Hanson
Lehigh Cement Company is among the leading producers of bulk and bagged cement in North America With plants and distribution terminals strategically located across the United States and Canada, we manufacture and distribute a variety of cements and cementitious materials Lehigh products cover a range of ordinary portland cement for traditional uses as well as blended cement (slag, fly ash Cement production in the United States has a substantially large and wellestablished base with 1205Mt per year, according to United States Geological Survey (USGS) Cement is produced either from integrated plants or grinding plants, but most of the USA production are from the former one The cement production in the USA is mostly controlled by []10 Largest Cement Companies in the USAHeidelbergCement is the largest cement company in Germany, and the company currently employs 55,047 throughout its operations Heidelberg Cement is primarily known for manufacturing concrete, asphalt, cement, aggregates Lehigh Hanson was established in the year 1887 in the USA as a cementproducing companyTop 10 Cement Companies in USAClinker is a nodular material produced in the kilning stage during the production of cement and is used as the binder in many cement products The lumps or nodules of clinker are usually of diameter 325 mm and dark grey in color It is produced by heating limestone and clay to the point of liquefaction at about 1400°C1500°C in the rotary kiln What is Cement Clinker? Composition, Types Uses Civil Feb 15, 2021 Cement production reached an estimated 90 million metric tons in the United States in 2020, in comparison to the 41 billion metric tons of cement produced worldwideUS and world cement production 2020 Statista
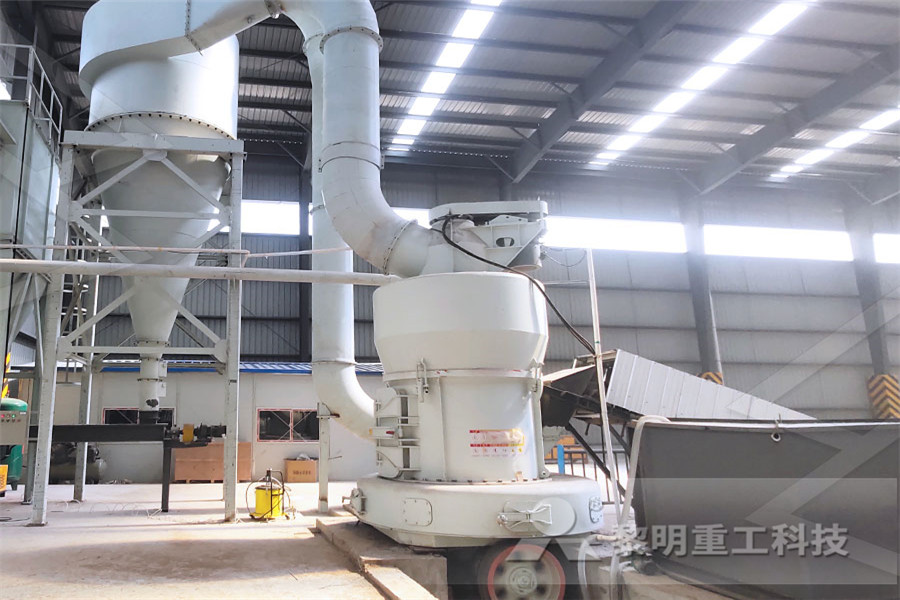
Cement Market Size, Share, Trends and Industry Forecast to
The Global Cement Market production capacity stood at 522 billion tons in 2018 And is expected to register a CAGR of 62% during the forecast period from 2019 to 2025, Cement is a binding agent used for joining or hold of different materials, usually fine powders of inorganic materials with key constituents as limestones, calcium silicate, chalk, shells, and othersFeb 28, 2021 JK cement planned to invest Rs 1,700 crore (US$ 2467 million) to increase its production capacity to 15 million tonnes by end of 2020 In November 2020, Shiva Cement Ltd, a subsidiary of JSW Cement Ltd, has announced plans to invest over Rs 1,500 crore (US$ 20321 million) in a new 136 million tonne per annum clinker unit project in Odisha Cement Industry in India, Indian Cement Industry, Sector Sep 16, 2019 It’s well known that the production of cement — the world’s leading construction material — is a major source of greenhouse gas emissions, accounting for about 8 percent of all such releases If cement production were a country, it would be the world’s thirdlargest emitterNew approach suggests path to emissionsfree cement MIT