Case
lling of kiln in cement plant
2022-07-11T13:07:09+00:00
Cement production and cooling Solex
May 04, 2020 The powder entering the kiln is heated to approximately 1,450ºC At these high temperatures, chemical reactions occur that form the cement clinker Upon exiting the kiln, the cement clinker is cooled to approximately 80ºCThe thermal efficiency of a cement cooler refers to the percentage of the total heat recovered from the hightemperature clinker and the physical heat of the clinker The higher the thermal efficiency, the more heat is recovered, which can be used to preheat the combustion air in Cement Cooler Cement Equipment In Cement PlantCement Cement industries have kilns of length varying from 70 to 80 m where clinker generation occurs Typical Rotary Kiln surface temperature in a cement industry varies from 150 deg C to 400 deg C The energy from the rotary kiln at temperatures around 150400 deg Celsius Cement Waste Heat Recovery from Cement Kiln – Radiant Jan 15, 2016 WHAT ARE THE MAIN PROCESS PROBLEMS IN CEMENT PLANT? In Pyroprocessing Cyclone Jamming Kiln inlet jamming Big clinker ball formation Coating formation in kiln Feed rushes and dusty kiln Snow man formation in cooler Red river in clinker cooler 01/15/16 3 Main reasons Uneven distribution of cooling air Mis alignment of kiln cooler 12 Process problems trouble shooting in cement kilnAbout 80% of the energy consumption for cement production is at the rotary kiln system for the clicker production These rotary kiln systems have to be maintained at high temperatures of 900 °C – 1500 °C More than 40% of the input energy is lost through the kiln shell, cooler stacks and kiln exhaust gases When all the heat losses are Waste Heat Recovery from Cement Kiln – Radiant Cooling
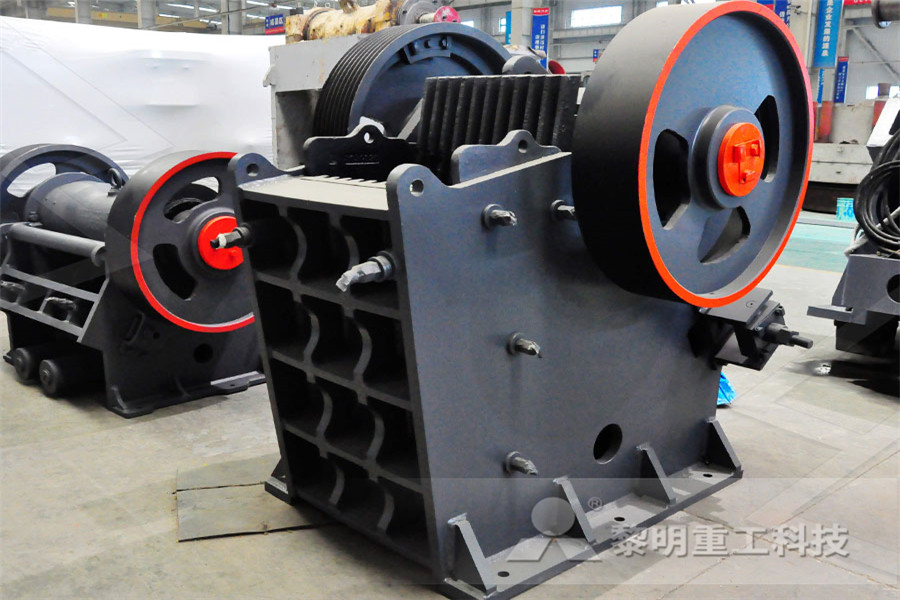
Failure of a Kiln Burner at a Cement Plant » Approved
May 24, 2017 The operation for Kiln 3 at a cement plant was stopped at 1125pm due to red spot (brick failure)Investigation indicates that the air channel pipe was “missing”, which resulted in a distorted flame shape This is because the primary function of the air channel pipe is said to shape the flame and swirl the air whilst introducing the coal dust, to enable efficient combustionDec 05, 2020 re Kiln shell cooling fans arrangment In today's cement plant we can see both ways of placing the shell cooling fans ie on charge side and in some plants in opposite side of charge But practically it has seen that fans placed on charge side has better effect on formation of coating It is a kind of quenching effect on charge sideKiln shell cooling fans arrangment Page 1 of 1Accessing this course requires a login Please enter your credentials below!CEMENT KILN MAINTENANCE The Cement InstituteBucket Grate Coolers The first form of grate cooler used on British kilns was the Bucket Grate The cooler was built into a greatlyenlarged kiln hood, with length about 19 times the kiln diameter, and width 15% greater than the length A concave grateplate occupied Cement Kilns: Grate Coolers Cement Plants and Kilns in The hot clinker discharged from the kiln at a temperature of about 1300 C is further treated in clinker cooler The cooling of clinker influences its structure, main composition, grindability and consequently, the quality of the resulting cementCLINKER COOLING TECHNOLOGY Mechanical engineering
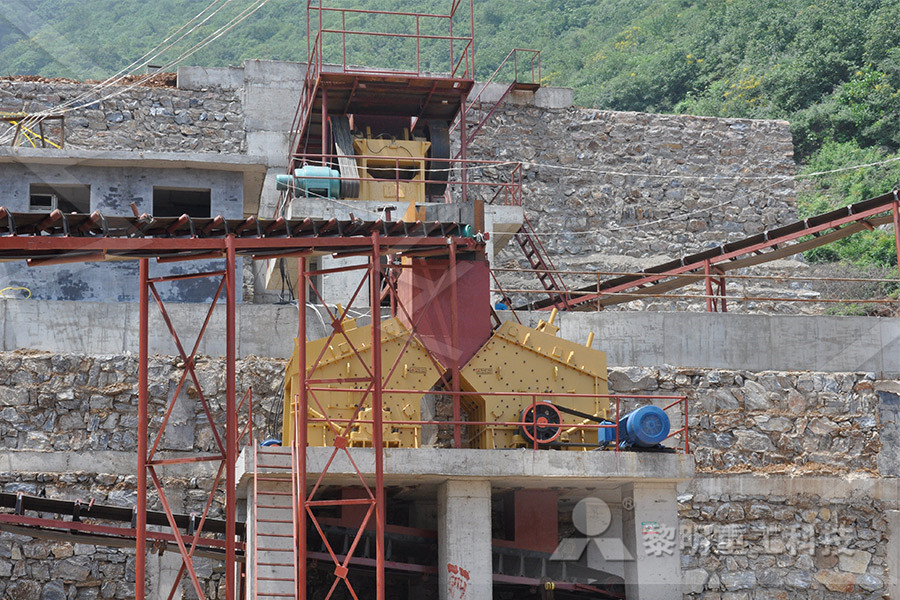
Clinker Cooler Cement Cooler AGICO Cooler In Cement Plant
In the calcination process of cement clinker, preheating, calcining, and cooling are three inseparable process links As the supporting equipment of cement rotary kiln, clinker cooler (also called cement cooler) is a kind of heat exchange device that transfers heat from hightemperature clinker to lowtemperature gasIt plays an important role in the cement clinker production process and Apr 15, 2018 Equipment used for creating the YouTube video:1 Smartphone: https://amznto/38ZP0xN2 Tripod: https://amznto/333La2K3 Laptop: httThe Cement Plant Rotary Kiln in Operation YouTubeof heat recovery in cement plants are flue gases, radiation from the outer surface of the rotary kiln, the heat carried by the hot clinker leaving the furnace and cooling air forUtilization of waste heat from rotary kiln for burning Cement industries have kilns of length varying from 70 to 80 m where clinker generation occurs Typical Rotary Kiln surface temperature in a cement industry varies from 150 deg C to 400 deg C The energy from the rotary kiln at temperatures around 150400 deg Celsius presently is Cement Waste Heat Recovery from Cement Kiln – Radiant About 80% of the energy consumption for cement production is at the rotary kiln system for the clicker production These rotary kiln systems have to be maintained at high temperatures of 900 °C – 1500 °C More than 40% of the input energy is lost through the kiln shell, cooler stacks and kiln exhaust gases When all the heat losses are Waste Heat Recovery from Cement Kiln – Radiant Cooling
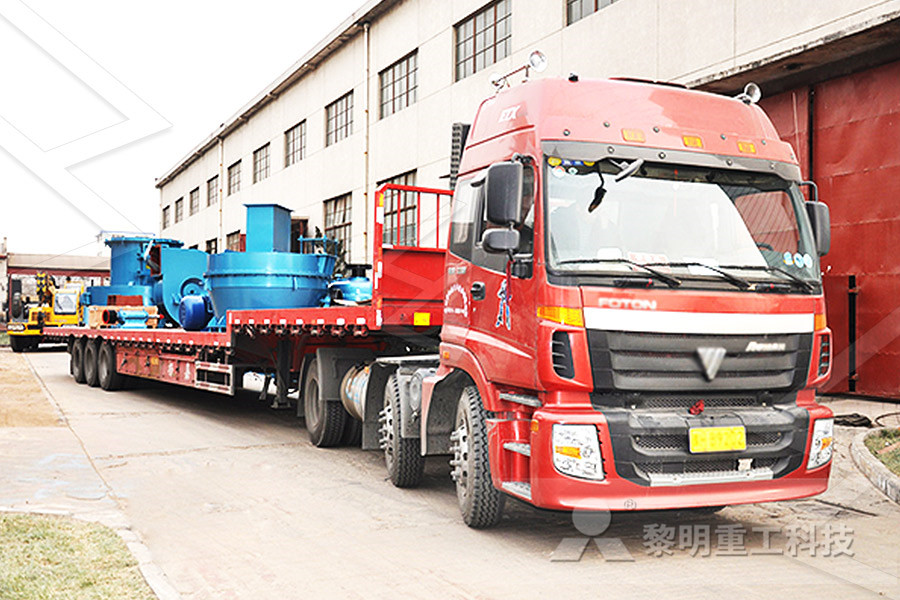
Gas Analysis on Cement Plants
Gas Analysis on Cement Plants, rev July 2008 Application The Kiln Inlet gas analysis system is especially designed for the highest temperatures and dust loads in cement production Typical applications are kiln inlet, riser duct, calciner and cyclone exit Jan 15, 2016 WHAT ARE THE MAIN PROCESS PROBLEMS IN CEMENT PLANT? In Pyroprocessing Cyclone Jamming Kiln inlet jamming Big clinker ball formation Coating formation in kiln Feed rushes and dusty kiln Snow man formation in cooler Red river in clinker cooler 01/15/16 3 Main reasons Uneven distribution of cooling air Mis alignment of kiln cooler 12 Process problems trouble shooting in cement kilnThis means that an efficient kiln consuming 32 GJ per tonne of clinker will only take in 1216 kg of air per tonne of clinker ie the air/clinker ratio is 1216 Using this air alone in the cooler would result in a clinker temperature of 399°C, so the extra air needed to obtain a reasonable temperature is surplus to Cement Kilns: Grate Coolers Cement Plants and Kilns in Cement Plants and Kilns in Britain and Ireland About this site About cement About clinker List of plants Map of plants Raw materials About Kilns Other technical advances Trends in innovation Sources Historical Texts Reference Essays Contact Site MapCement Plants and Kilns in Britain and IrelandThe kiln of the pyro processing plant is the heart of the cement plant Cement manufacturing processes, termed according to the condition of the feed entering the kiln, are Wet, Dry, Semi CEMENT MANUFACTURING PROCESS: BURNING TECHNOLOGY

How a kiln works in a cement plant? 2019! YouTube
How a kiln works in a cement plant? 2019! Prevent Hair Loss in 2 Weeks Supplement (GET FREE Bottle in India): toptrendyoffersga/provillusreviewThe Cement manufacturing: components of a cement plant This page and the linked pages below summarize the cement manufacturing process from the perspective of the individual components of a cement plant the kiln, the cement mill etc For information on materials, including reactions in the kiln, see the ' Clinker ' pagesCement manufacturing components of a cement plantCement industry uses large number of cooling fans usually between 5 to 15 in one clinker line based on the kiln capacity Cooling fans are used to blow cold air to the cooler and to cool the clinker from 1500oC to 100oC Cooling kiln protects equipment and facilitates quenching the clinker to ensure the important forms of minerals like C3S, C2S Process Fans Used in Cement Industry ReitzindiaIn the calcination process of cement clinker, preheating, calcining, and cooling are three inseparable process links As the supporting equipment of cement rotary kiln, clinker cooler (also called cement cooler) is a kind of heat exchange device that transfers heat from hightemperature clinker to lowtemperature gasIt plays an important role in the cement Clinker Cooler Cement Cooler AGICO Cooler In Cement PlantFeb 24, 2017 How a kiln works in a cement plant? 2019! Prevent Hair Loss in 2 Weeks Supplement (GET FREE Bottle in India): toptrendyoffersga/provillusreviewThe How a kiln works in a cement plant? 2019! YouTube

Cement Cooling System Efficient, Industrial Cement
The cooling of cement is an important step prior to storage in mitigating gypsum dehydration and subsequent moisture liberation which can lead to lump formation Recommendations vary but it is generally accepted that with mill outlet temperatures of around 110ºC – 120ºC, cooling to below 80ºC is necessary to avoid this reactionMay 20, 2020 Clinker/sinter cooling is one of the main operations in a cement plant and in a steel works sinter strand Whereas other processes may involve two to four large fans, cooling involves a greater number of fans with each fan blowing air through the sinter as it passes byCement Plant Superfans World CementCement manufacturing: components of a cement plant This page and the linked pages below summarize the cement manufacturing process from the perspective of the individual components of a cement plant the kiln, the cement mill etc For information on materials, including reactions in the kiln, see the ' Clinker ' pagesCement manufacturing components of a cement plantThe kiln of the pyro processing plant is the heart of the cement plant Cement manufacturing processes, termed according to the condition of the feed entering the kiln, are Wet, Dry, Semi CEMENT MANUFACTURING PROCESS: BURNING TECHNOLOGY AGICO CEMENT supplier rotary drum cooler in cement plant, grate cooler, and other clinker coolers for cement manufacturing High cooling performance and factory price, get your FREE quotation now!Rotary Cooler Clinker Cooler In Cement Plant AGICO CEMENT
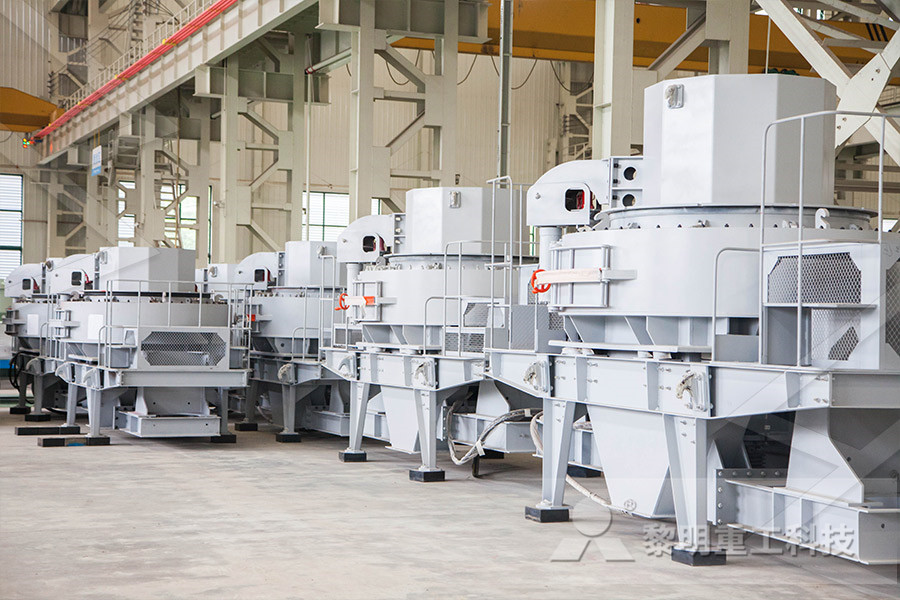
Waste Heat Recovery from Cement Kiln – Radiant Cooling
About 80% of the energy consumption for cement production is at the rotary kiln system for the clicker production These rotary kiln systems have to be maintained at high temperatures of 900 °C – 1500 °C More than 40% of the input energy is lost through the kiln shell, cooler stacks and kiln exhaust gases When all the heat losses are Gas Analysis on Cement Plants, rev July 2008 Application The Kiln Inlet gas analysis system is especially designed for the highest temperatures and dust loads in cement production Typical applications are kiln inlet, riser duct, calciner and cyclone exit Gas Analysis on Cement Plants1 Cooling Water: The major water use at most cement plants is for cooling Cooling water is used for bearings on the kiln and grinding equipment, air compressors, burner pipes and finished cement Most cooling is noncontact Cooling use is approximately the How to Treat Wastewater from Cement Ceramic Industry consumption, and frequently kiln or plant operational stops The energy penalty caused by the circulation phenomenon is believed to be significant but presently no reliable estimates are available Incomplete combustion of fuels in the calciner and/or kiln burner may lead to an increase in the Cl and especially Scirculation in cement plantsReview: Circulation of Inorganic Elements in Combustion of Cement clinker cooler and method for cooling cement clinker (22) 29102013 (43) 06052015 (57) White cement clinker can be efficiently produced using a kiln 10 for sintering cement clinker and unloading the cement clinker from the kiln 10 to a clinkerLatest trends in clinker cooling Cement Lime Gypsum
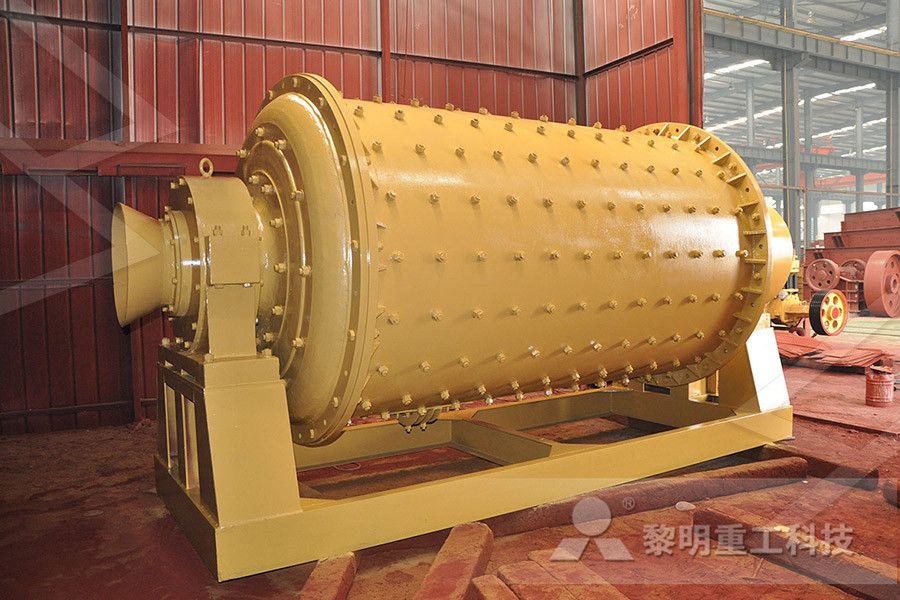
WASTE HEAT RECOVERY SYSTEM (WHRS) FOR CEMENT
Key words:Cement Plant, Rotary kiln system, Energy Balance, Heat Balance, Heat Recovery Abstract Waste Heat Recovery (WHR) is the process of recovering heat dischargedas a byproduct of one process to provide heat needed by a second process So it is the capture and the use ofvi Improving Thermal and Electric Energy Efficiency at Cement Plants: International Best Practice Cement is paramount for economic development and poverty reduction in emerging markets Along with aggregates and water, cement is the key ingredient in the production of concrete, and, as such, is an essential construction materialIMPROVING THERMAL AND ELECTRIC ENERGY