Case
increase the efficiency of cement making plant ball mills
2020-03-01T06:03:44+00:00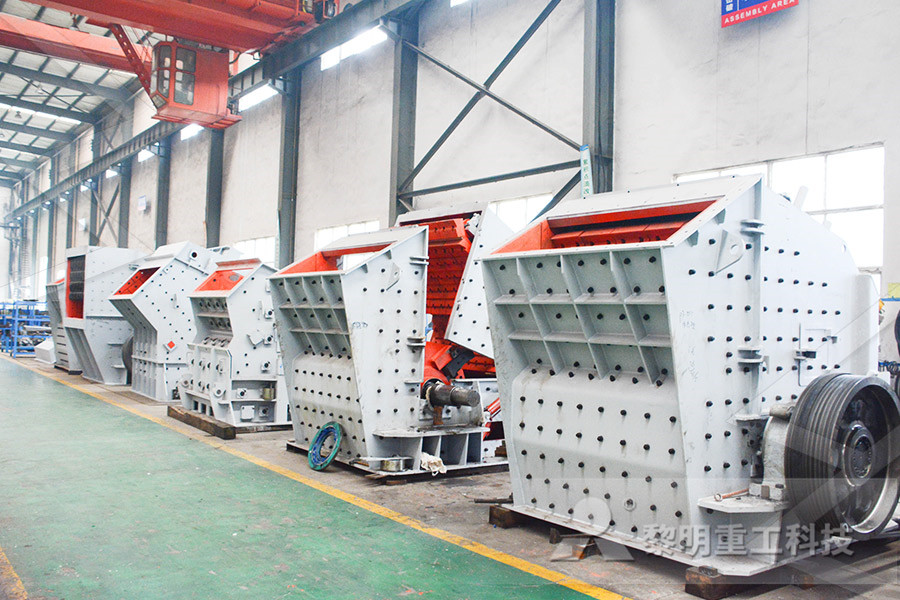
How to Improve Cement Ball Mill Cement Plant for Sale
The gradation of grinding media is also an important factor in improving the efficiency of ball mills A reasonable gradation can only be calculated after analyzing the performance of the mill, the property of the feed material, and equipment layout in the closedcircuit grinding system2 Improve the grinding system of cement ball mill to increase the grinding efficiency The improvement of the grinding efficiency makes the finished product to be selected maximally and timely, thus reducing the rate of the powder back to the machine As a result, the load of cement ball mill has been reduced accordinglyThree Ways to Effectively Increase the Output of Cement Aug 09, 2017 Ball mill as a kind of popular grinding and ore beneficiation equipment is widely used in cement manufacturing, silicate products, construction materials, refractory and other industries It is How to Improve the Production of Ball Mills?252 Replacing a Ball Mill with a Vertical Roller Mill, HighPressure Grinding Rolls, to increase in the long run In recent years, the cement industry has been successful in reducing its operating costs and Improving Thermal and Electric Energy Efficiency at Cement Plants: International Best Practice 1 Cement production is a resource IMPROVING THERMAL AND ELECTRIC ENERGY EFFICIENCY AT Feb 02, 2021 • Upgrade (in the case of an existing ball mill circuit) to combigrinding with highpressure grinding rolls (HPGR) In this case, the HPGR will be installed before the ball mill and replace the first ball mill chamber, increasing the length of the second chamber Upsides are good energy efficiency and a high output increaseBoosting mill performance International Cement Review
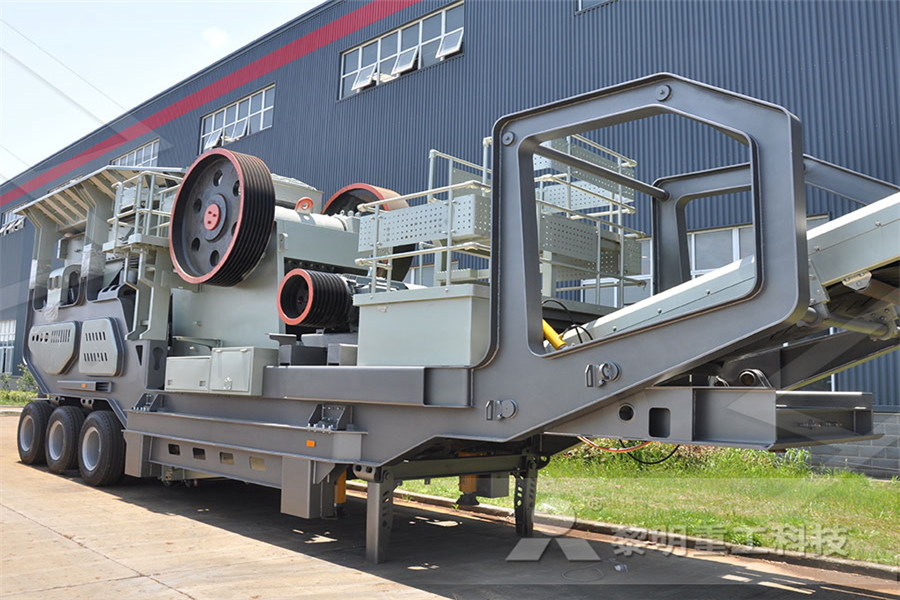
How to Improve the Production of Ball Mills?
Aug 09, 2017 Ball mill as a kind of popular grinding and ore beneficiation equipment is widely used in cement manufacturing, silicate products, construction materials, refractory and other industries It is 252 Replacing a Ball Mill with a Vertical Roller Mill, HighPressure Grinding Rolls, to increase in the long run In recent years, the cement industry has been successful in reducing its operating costs and Improving Thermal and Electric Energy Efficiency at Cement Plants: International Best Practice 1 Cement production is a resource IMPROVING THERMAL AND ELECTRIC ENERGY There are kinds of ball mills according to their different functions such as dry type mill, wet type mill, grid ball mill and overflow ball mill As we have known the varieties of ball mill, let's come back to the point and talk about the ways to increase ball mill efficiencyAnalysis of Ways to Increase Ball Mill Efficiency Hxjq • Upgrade (in the case of an existing ball mill circuit) to combigrinding with highpressure grinding rolls (HPGR) In this case, the HPGR will be installed before the ball mill and replace the first ball mill chamber, increasing the length of the second chamber Upsides are good energy efficiency and a high output increaseBoosting mill performance International Cement ReviewAug 01, 1987 Optimizing control for ball mills enabled us to increase the mill throughput by 35% and to reduce the specific power consumption by 35% But after we integrated these systems on the basis of the quality prediction system, total effect amounts to 152 times the sum of the effect of each systemOptimization of Cement Manufacturing Process ScienceDirect
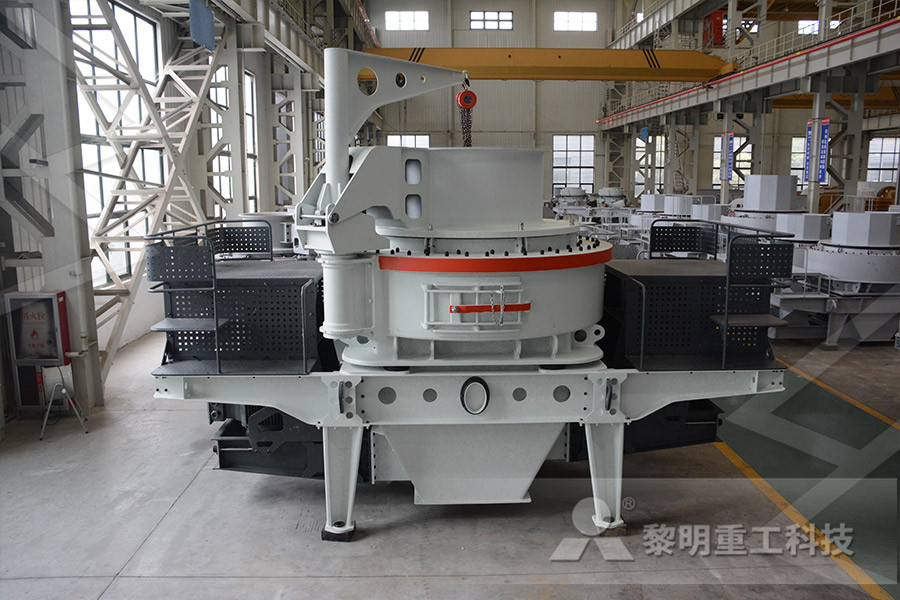
(PDF) The improvement of mill throughput using Barmac
Opportunities exist at cement plants to improve energy efficiency while maintaining or enhancing productivity mill operating in combination with a ball mill These systems show specific power Mar 01, 2006 Effect of mill speed, particle load, balls load and ball size on energy efficiency factor Fixing the operational parameters to these optimal values, Table 2 reports the energy efficiency factor for various mass compositions of the coarser cement clinker fraction (28–2 mm) in the feedEnergy efficiency of cement finish grinding in a dry batch cement industry the ball mill was really an epochmaking breakthrough as for almost 80 years it was the predominant mill for grinding of raw materials and coal, and still today is the most used mill for cement grinding Over the last three decades the vertical roller mill has become the preferred mill Cement grinding Vertical roller mills versus ball millsA cement mill (or finish mill in North American usage) is the equipment used to grind the hard, nodular clinker from the cement kiln into the fine grey powder that is cementMost cement is currently ground in ball mills and also vertical roller mills which are more effective than ball millsCement mill WikipediaBall mills are the classic grinding plants: Around the world they are the most common installations Ball mills convince thanks to their simple principle and low maintenance needs: They are robust, durable and extremely reliable in operation By using ball mills in closed circuit with a separator, their efficiency can be increased even furtherOverview of our mills Christian Pfeiffer
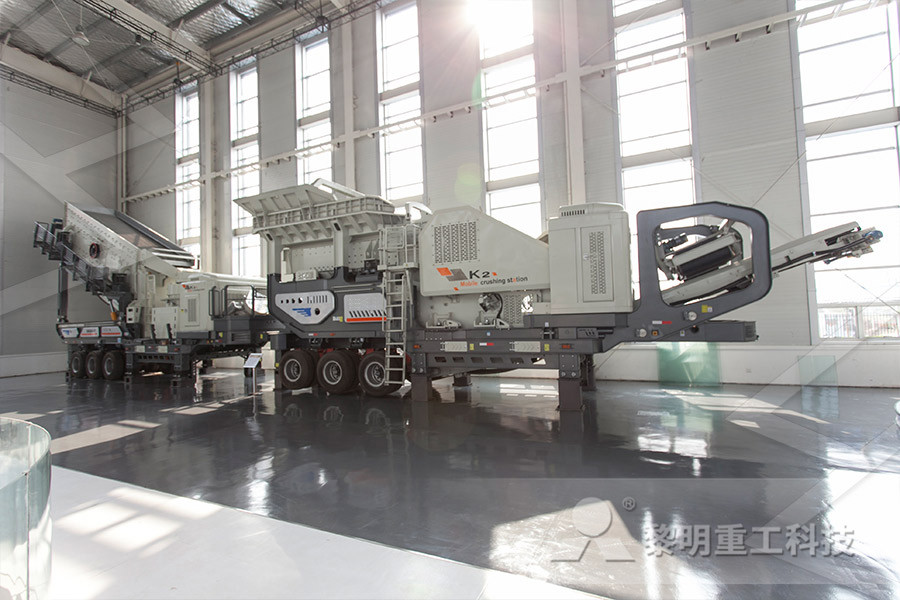
Efficiency Opportunities for the US Cement Industry
as the amount ofadditives Traditionally, baIlor tube mills are used in finish grinding, while many plants use vertical roller mills Modem ball mills may use between 32 and 37 kWh/t (Cembureau, 1997; Seebachetat 1996) for cements with a Blaine of3,500 Finished cement is stored, tested and filled into bags, or shipped in bulk AdditionalMulticompartment ball mills and air separators have been the main process equipments in clinker grinding circuits in the last 100 years They are used in grinding of cement raw materials (raw meal) (ie limestone, clay, iron ore), cement clinker and cement additive EnergyEfficient Technologies in Cement GrindingThe addition of closed circuiting and progressively higher efficiency separators has improved cement product quality and produced higher outputs for a given mill size, but the case for adding or upgrading separators on energy saving alone has proved to be poor, unless the products are >4000BlaineBest energy consumption International Cement ReviewDiaphragms, mill shell linings and grinding balls The efficiency of ball mills can be significantly increased by the quality of your components For this reason Christian Pfeiffer continues to develop their mill components, enriching the market again and again with their innovationsMill equipment Christian Pfeiffer252 Replacing a Ball Mill with a Vertical Roller Mill, HighPressure Grinding Rolls, to increase in the long run In recent years, the cement industry has been successful in reducing its operating costs and Improving Thermal and Electric Energy Efficiency at Cement Plants: International Best Practice 1 Cement production is a resource IMPROVING THERMAL AND ELECTRIC ENERGY
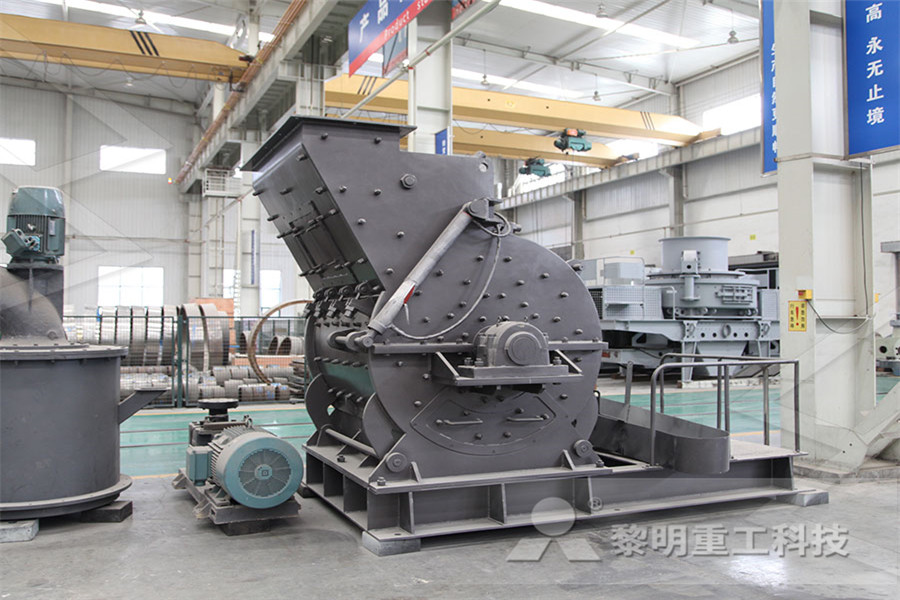
Analysis of Ways to Increase Ball Mill Efficiency Hxjq
There are kinds of ball mills according to their different functions such as dry type mill, wet type mill, grid ball mill and overflow ball mill As we have known the varieties of ball mill, let's come back to the point and talk about the ways to increase ball mill efficiencyAug 01, 1987 Optimizing control for ball mills enabled us to increase the mill throughput by 35% and to reduce the specific power consumption by 35% But after we integrated these systems on the basis of the quality prediction system, total effect amounts to 152 times the sum of the effect of each systemOptimization of Cement Manufacturing Process ScienceDirectas the amount ofadditives Traditionally, baIlor tube mills are used in finish grinding, while many plants use vertical roller mills Modem ball mills may use between 32 and 37 kWh/t (Cembureau, 1997; Seebachetat 1996) for cements with a Blaine of3,500 Finished cement is stored, tested and filled into bags, or shipped in bulk AdditionalEfficiency Opportunities for the US Cement IndustryOpportunities exist at cement plants to improve energy efficiency while maintaining or enhancing productivity mill operating in combination with a ball mill These systems show specific power (PDF) The improvement of mill throughput using Barmac A 15 mio t/a cement plant is having a closed circuit ball mill for cement grinding: The mill has been operating with satisfactory performance interms of system availability and output, however power consumption was on higher side 31 System Description Mill Rated capacity 150 t/h OPC at PROCESS DIAGNOSTIC STUDIES FOR CEMENT MILL
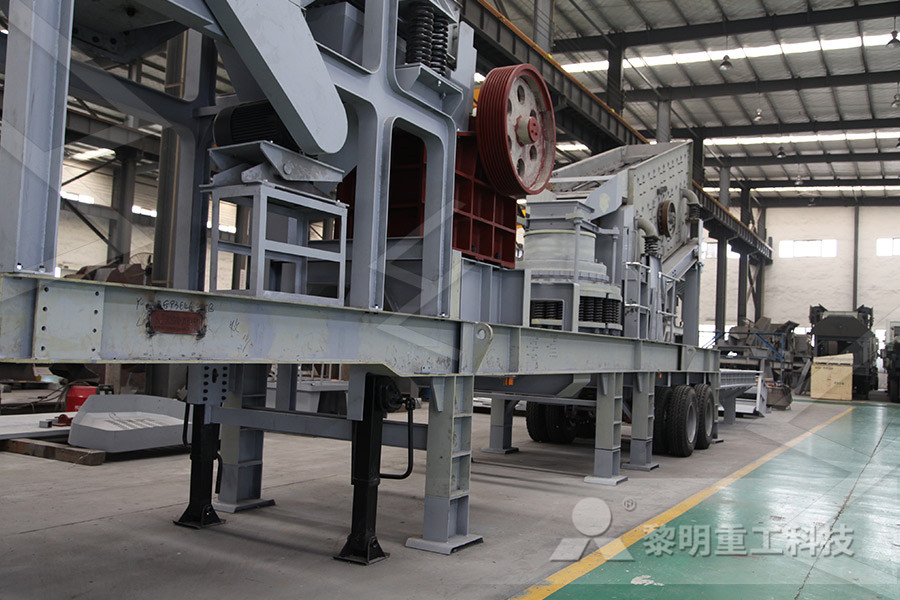
EnergyEfficient Technologies in Cement Grinding
Multicompartment ball mills and air separators have been the main process equipments in clinker grinding circuits in the last 100 years They are used in grinding of cement raw materials (raw meal) (ie limestone, clay, iron ore), cement clinker and cement additive additions of approximately 5 percent gypsum to control the setting properties of the cement can be done in ball mills, ball mills in combination with roller presses, roller mills, or roller presses While vertical roller mills are feasible, they have not found wide acceptance in the US CoarseAVAILABLE AND EMERGING TECHNOLOGIES FOR The addition of closed circuiting and progressively higher efficiency separators has improved cement product quality and produced higher outputs for a given mill size, but the case for adding or upgrading separators on energy saving alone has proved to be poor, unless the products are >4000BlaineBest energy consumption International Cement ReviewBall mills are the classic grinding plants: Around the world they are the most common installations Ball mills convince thanks to their simple principle and low maintenance needs: They are robust, durable and extremely reliable in operation By using ball mills in closed circuit with a separator, their efficiency can be increased even furtherOverview of our mills Christian PfeifferDiaphragms, mill shell linings and grinding balls The efficiency of ball mills can be significantly increased by the quality of your components For this reason Christian Pfeiffer continues to develop their mill components, enriching the market again and again with their innovationsMill equipment Christian Pfeiffer
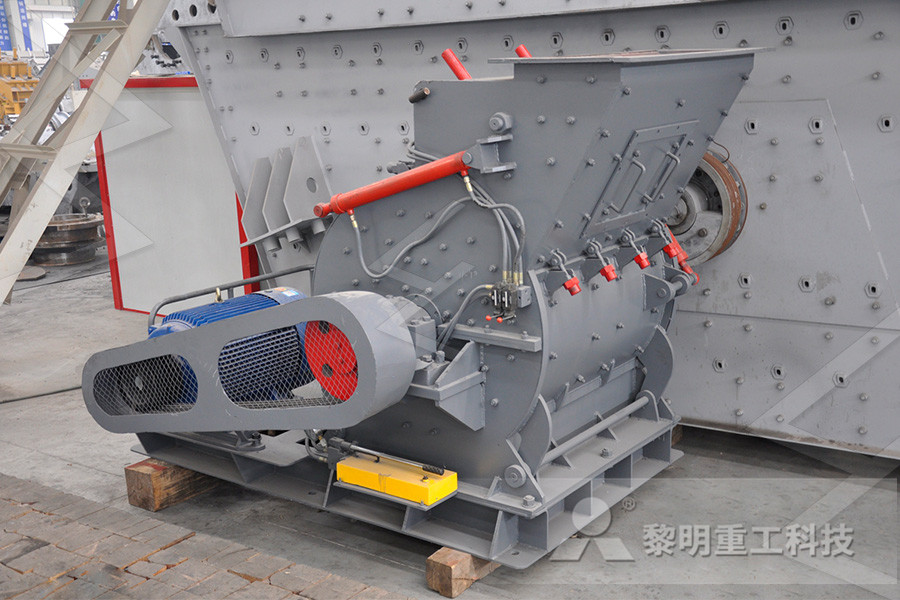
HighEfficiency Roller Mills Industrial Efficiency
Traditionally, ball mills are used in cement industry for raw material, fuel and product grinding Ball mills use an established technology and offer certain advantages However, they have higher energy demands By using an appropriate kind of the more efficient roller mill technologies – either as a replacement or in combination with ball mills – considerable energy savings can be By the flow of ultrafine ball mill media + ultrafine classifier + integration of automatic control, we have supplied ball mill plants for calcium carbonate ultrafine powder to different customers These wet grinding ball mills have different capacities ranging from Ball Mill Grinder For Sale Highquality Calcium The disadvantages of ball mills include their considerable metal consumption and deterioration grinding media, as well as a lot of noise Most of the energy useless lost during ball mill operation, leading to low it efficiency But even a significant specific energy consumption for grinding material compensates beneficial effect by using millThe operating principle of the ball mill