Case
simple ball mill filling level
2022-12-02T05:12:08+00:00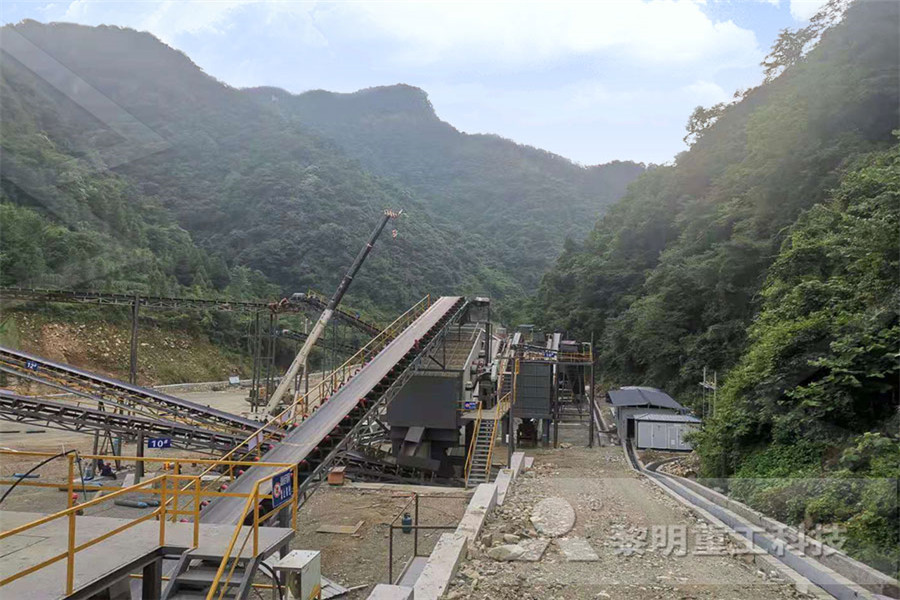
ball mill fill level strain gauges provesprojektde
Ball mill fill level strain gauge thierry albert be feature extraction of a straingauge signal using in this work, a method for the measurement of the apparent filling level in a pilot ball mill, the continuous charge measurement system ccm has been used the technique uses a strain gauge sensor, mounted on a flat steel spring, which is fitted into a recess underneath a lifter bar Since delivery time for parts to repair the damaged drive was lengthy, a decision was made to reduce the charge in the ball mill from approximate 32% filling level to a point low enough to allow the mill to be operated with the single remaining drive Surprisingly the result was a minimal loss in production, with a significant gain in efficiencyEfficiency and grinding media filling level IEEE to ball filling variation in the mill The results obtained from this work show, the ball filling percentage variation is between 12– 37% which is lower than mill ball filling percentage, according to the designed conditions (15%) In addition, acquired load samplings result for mill ball filling was 13%A Method to Determine the Ball Filling, in Miduk Copper
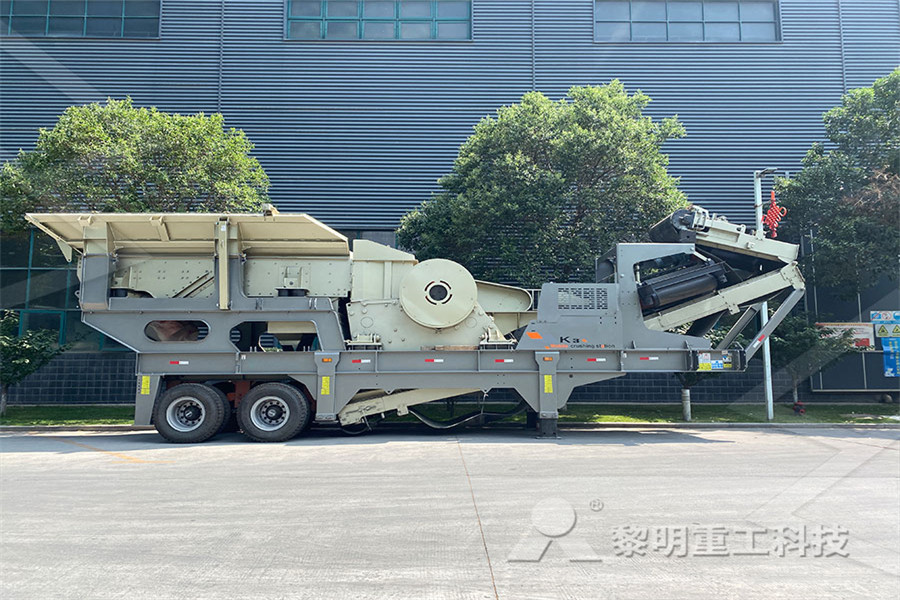
Optimization of mill performance by using
indicator of ball filling degree and, often, try to keep it at the maximum level It is well known that the mill absorbed power depends on operating parameters other than ball level, such as pulp density and liner configuration Figure 2 shows that there is no linear relation between mill absorbed power and ball filling degree As indicated on tioning of a ball mill and improving its performance and its power efficiency With the above objective on the background, surveys have been realized in a South African platinum mine (AngloPlatinum) by varying the density, the filling degree J and the liners wear on a secondary ball mill equipped with a SensomagImproving the Grinding Performance of Ball Mills with a There are two factors which make extremely difficult to correlate experimentally torque and filling level in a ball mill One of them is a saturation effect appearing on torque as the mill filling increases The other factor is the effect of the gears, always present to multiply the torque of the electric drive, which smear torque signal with Frequency domain characterization of torque in
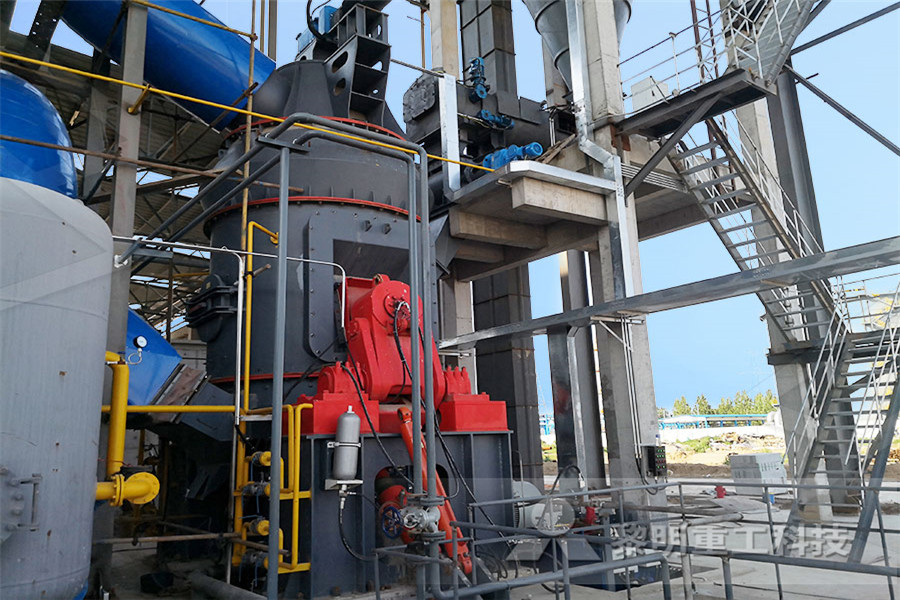
EFFECT OF PARTICLE FILLING AND SIZE ON THE
Figure 41 Photograph of the mill and the installation of inductive proximity probe 71 Figure 42 Photographs of the coarse and fine particles72 Figure 43 Variations in net power draw with particle filling at different mill speeds for a ball filling of 20% 74 Figure 44 Inductive probe’s signal, ball CAD Detail Files Free Architectural CAD drawings and blocks for download in dwg or pdf file formats for designing with AutoCAD and other 2D and 3D modeling software By downloading and using any ARCAT content you agree to the following [ license agreement ]Download Free CAD Drawings, AutoCad Blocks and Ball mill fill level electronic ear location In Single chamber ball mill for clinker grinding what is optimim locaion for electronic ear for measuring ball mill fill level best regards pks Reply Know the answer to this question? Join the community and register for a free guest account to post a replyBall mill fill level electronic ear location Page 1 of 1
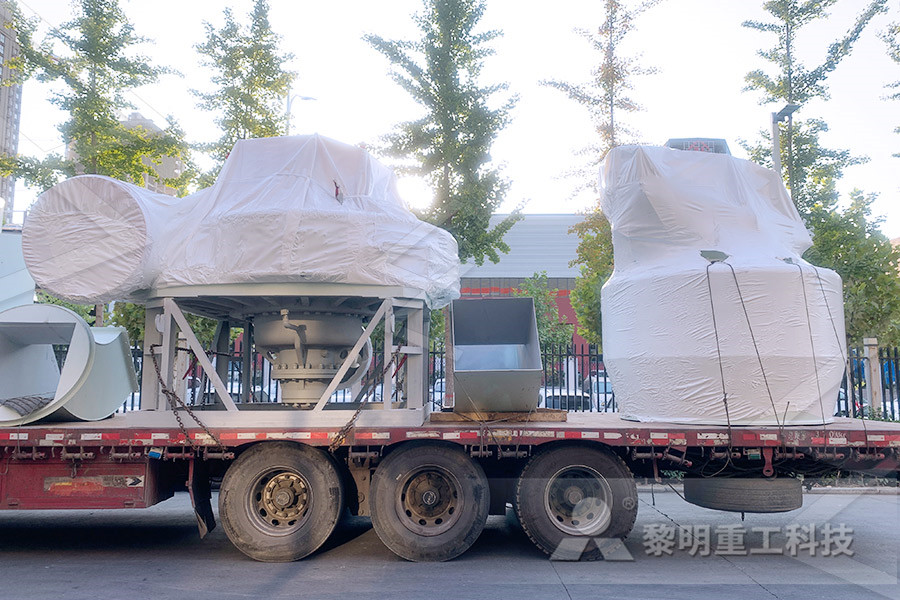
Optimization of mill performance by using
indicator of ball filling degree and, often, try to keep it at the maximum level It is well known that the mill absorbed power depends on operating parameters other than ball level, such as pulp density and liner configuration Figure 2 shows that there is no linear relation between mill absorbed power and ball filling degree As indicated on With this information, the Sensomag can determine the ball filling degree The surveys consisted in varying the filling degree (25%, 30%, 33%) and for each value of J, the solid density was varied from 65% to 75% (average values) The mill was relined ahead of Improving the Grinding Performance of Ball Mills with a The Ball MillScan utilises the latest in digital signal processing techniques available to provide an accurate of the change in the mill fill level (vectors) The system is made up of 1 wireless shell sensor and 2 wired inlet/outlet sensors The signals may be used in Ball MillScan Process IQ
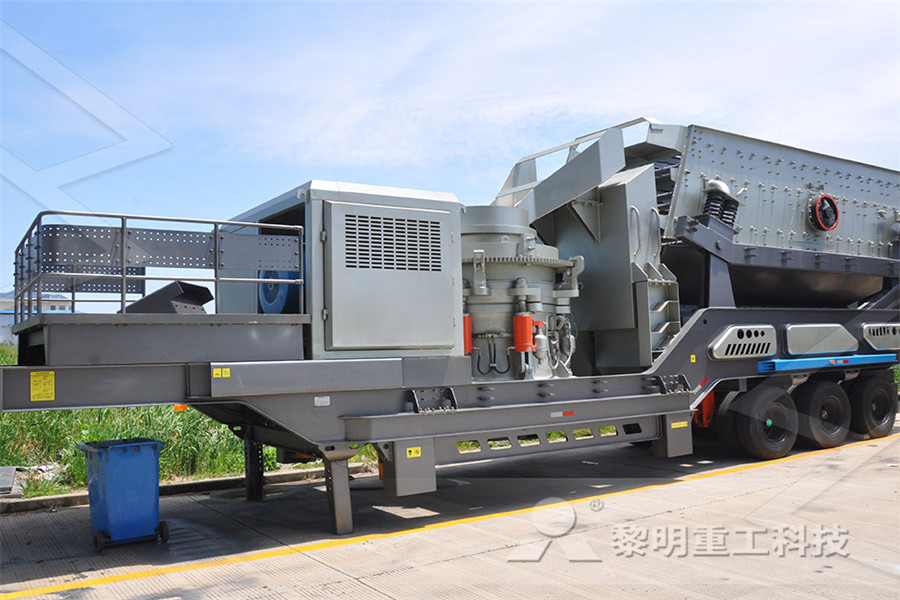
Dynamic Modelling of Temperature in a Wet Ball Mill
The mill measured 73 m diameter by 96 m long Under normal operating conditions, the mill ball filling is 30% of total mill volume, mill speed is 75% of critical speed, solids concentration in slurry is 75%, solids feed rate is 330 tph and rated power draw is 9500 KWThe question about modern intelligent information processing methods usage for a ball mill filling level evaluation is considered Vibration acceleration signal has been measured on a mill laboratory model for that purpose It is made with accelerometer attached to a mill pin The conclusion is made that mill filling level can not be measured with the help of such signal amplitude onlyStudy on Neural Networks Usage to Analyse respectively The mill was configured to operate as a RoM ball mill The experiments were conducted at varying mill speeds (75%85% critical speed), feed rate (12002800kg/hr) and ball loads (1526%) The static mill filling was determined from physical measurements after crash stopping the millOnLine Sensors for measuring the total Ball and charge
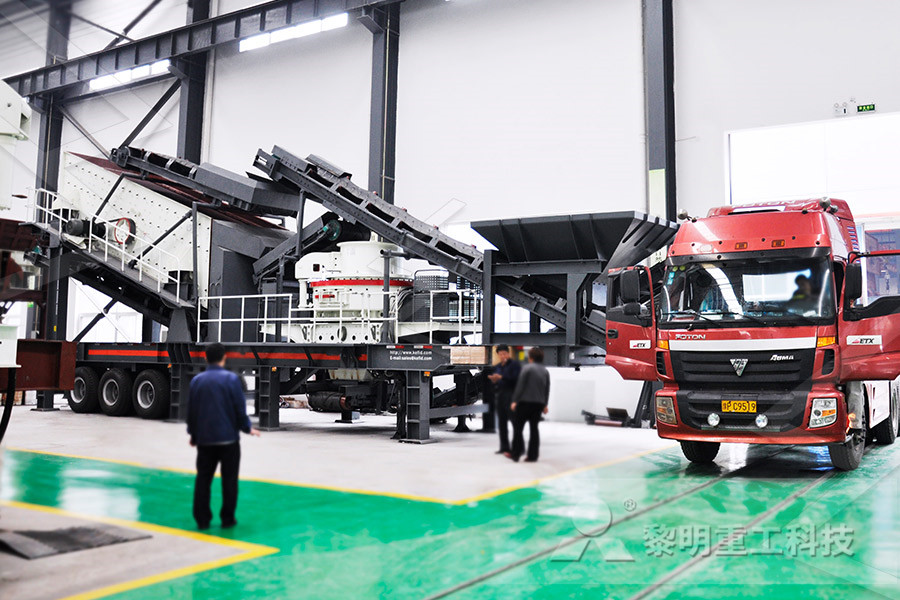
Effects of grinding media shapes on load behaviour
The variations of toe and shoulder positions with load filling (J) are shown in Fig 4, Fig 5, Fig 6The shoulder positions increased with increase in mill speed and charge filling and are in agreement with previous findings (Liddell and Moys, 1988, Moys and Skorupa, 1993)The toe positions were steady with mill speed up to about 60% criticalMOLOSwave level measurement Continuous level measurement with guided wave radar MOLOSsafe SFA Silo filling device – basic module of the silosafesystem MOLOScode electronically coded couplings MOLOSpressdec pressure indicator MSDA for silos Reliable protection against too high overpressure during the pneumatic filling processMOLLET, filling level, limit switch, level control, silo The starting point for ball mill media and liquid charging is generally as follows: 50% media charge Assuming 26% void space between spherical balls (nonspherical, irregularly shaped and mixedsize media will increase or decrease the free space) 50% x 26% = 13% free space Add to this another 45% to 50% above the ball Ball Mill Loading Wet Milling Paul O Abbe
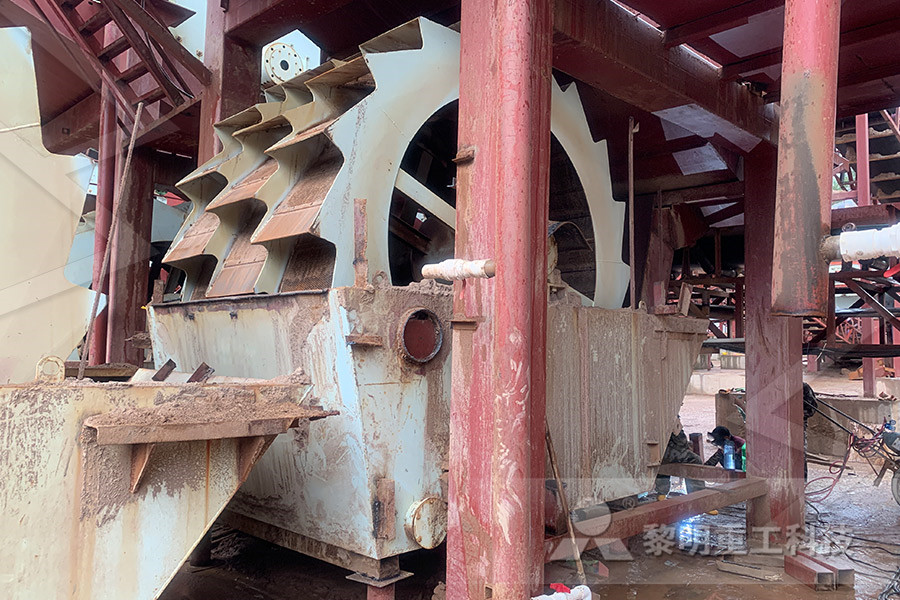
Pump tank – level measurement VEGA
Some of the balls from the mill can potentially enter the tank along with the slurry To prevent this from happening, the balls are collected in a weir arrangement, which overflows into the main tank Level measurement in the tank avoids dry running of the pump and ensures a continuous process Ball mills are a special instrument used to break up hard solids into a fine powder They are similar to rock tumblers in that the instrument is a rotating container filled with heavy balls to grind the substance into powder Ceramic material, crystalline compounds, and even some metals can be ground up using a ball millHow to Make a Ball Mill: 12 Steps (with Pictures) MOLOSwave level measurement Continuous level measurement with guided wave radar MOLOSsafe SFA Silo filling device – basic module of the silosafesystem MOLOScode electronically coded couplings MOLOSpressdec pressure indicator MSDA for silos Reliable protection against too high overpressure during the pneumatic filling processMOLLET, filling level, limit switch, level control, silo
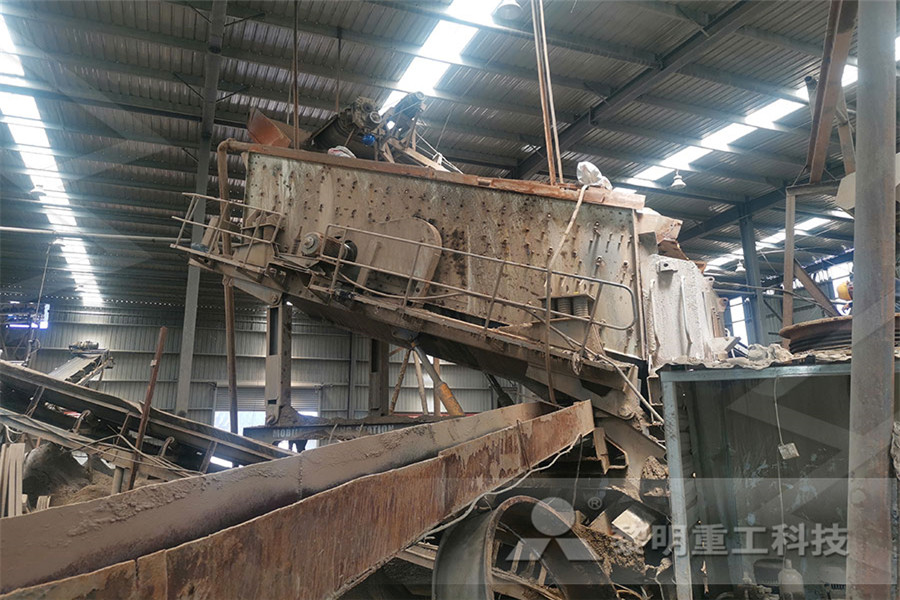
Online SAG Mill Pluse Measurement and Optimization
@article{osti, title = {Online SAG Mill Pluse Measurement and Optimization}, author = {Rajamani, Raj and Delgadillo, Jose and Duriseti, Vishal}, abstractNote = {The grinding efficiency of semi autogenous milling or ball milling depends on the tumbling motion of the total charge within the mill Utilization of this tumbling motion for efficient breakage of particles depends on the The ball to charge ratio may be 5:1, 10:1, 15:1 This method is more efficient in achieving fine particle size Rod mills: Horizontal rods are used instead of balls to grind Granularity of the discharge material is 4010 mm The mill speed varies from 12 to 30 rpm Planetary mill: High energy mill widely used for producing metal, alloy, and Powder metallurgy – basics applications ONLINE SAG MILL PULSE MEASUREMENT AND OPTIMIZATION Technical Report Rajamani, Raj ; Delgadillo, Jose ; Duriseti, Vishal The grinding efficiency of semi autogenous milling or ball milling depends on the tumbling motion of the total charge within the mill Utilization of this tumbling motion for efficient breakage of particles depends on the Online SAG Mill Pluse Measurement and Optimization

PolyKombo Liners Polycorp
The noise level around the mill is reduced The mill availibility is improved with PolyKombo™ Liners due to: Faster installation as it has less peening points Better fit against mill shell, avoiding cracks on shell plate due to high bolt torque and ball impacts Apparent Volumetric Ball Filling Level, expressed as a percentage of the net internal mill volume (inside liners) Necessarily less or equal than the Total Charge Filling (Cell F14) This value represents the Volumetric Fractional Filling of the Voids in between the balls and the rocks by the retained slurry in the mill chargePontificia Universidad Católica de ChileDepending on mill design, the setpoint may be a compromise between best breakage conditions (high sound level) and limiting liner damage due to ball strikes (low sound levels) For any particular mill filling, there is a mill speed which will maintain the setpoint sound level X ] » creativityengineered I N N O V A T I O N [ X