Case
the ball mill inside the process plant
2020-04-17T05:04:50+00:00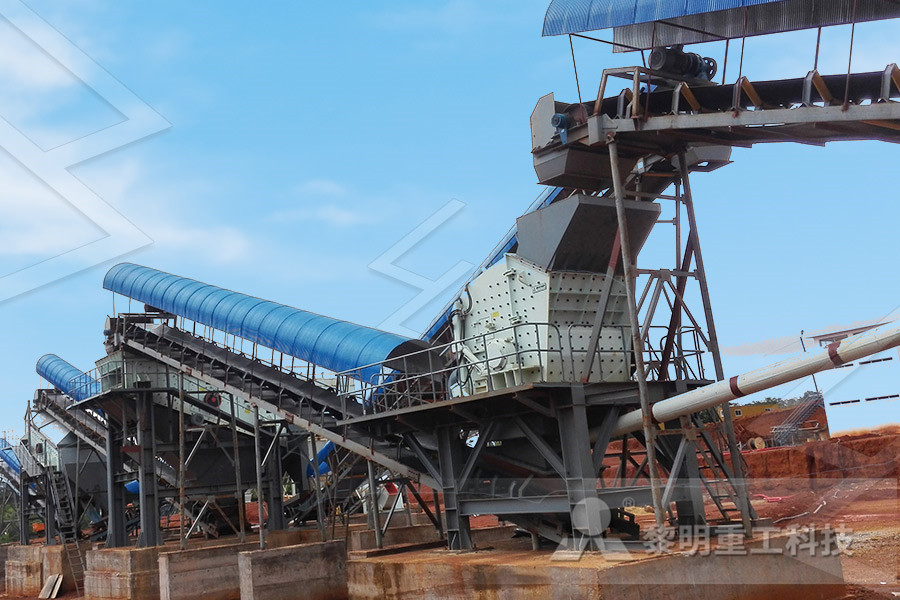
Ball Mills Industry Grinder for Mineral Processing
The ball miller machine is a tumbling mill that uses steel milling balls as the grinding media, applied in either primary grinding or secondary grinding applications Where the finished product does not have to be uniform, a ball mill may be operated in open circuit, but where the finished product must be uniform it is essential that the grinding mill be used in closed circuit with a screen, if a coarse product is desired, and with a classifier if a fine product is required In most cases it is desirable to operate the grinding mill Ball Mills 911 Metallurgist The operating principle of the ball mill consists of following steps In a continuously operating ball mill, feed material fed through the central hole one of the The operating principle of the ball mill
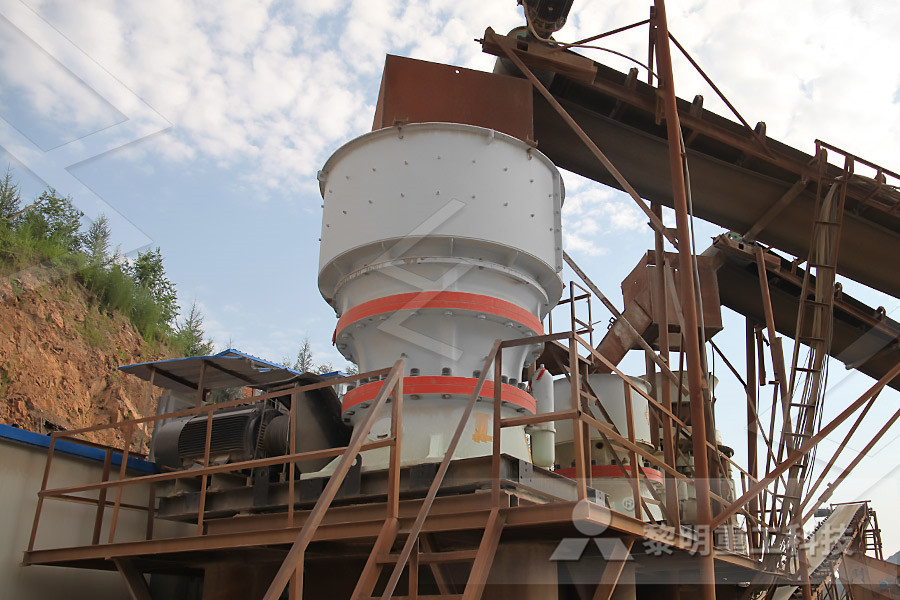
Ball Mill an overview ScienceDirect Topics
The ball mill is a tumbling mill that uses steel balls as the grinding media The length of the cylindrical shell is usually 1–15 times the shell diameter (Figure 811) The feed can be dry, with less than 3% moisture to minimize ball coating, or slurry containing 20–40% water by weight The ball mill is a key equipment to grind the crushed materials, which is widely used in the manufacture industries, such as cement, silicate, new building material, refractory material, fertilizer, ferrous metal, nonferrous metal and glass ceramics Ball Mill Machine Abstract: This paper introduces the development and implementation of a ball mill grinding circuit simulator, NEUSimMill Compared to the existing simulators in this field which focus on process flowsheeting, NEUSimMill is designed to be used for the test and verification of grinding process control system including advanced control system such as integrated controlModeling and Simulation of Whole Ball Mill Grinding
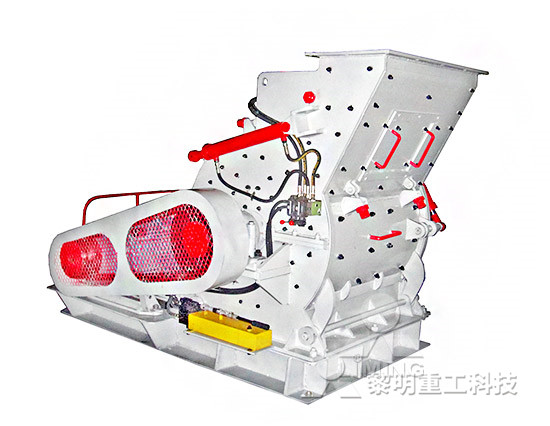
A guide to maximising ball mill circuit classification
the pump and cyclone system reengineering process in the context of ball mill circuit optimisation With a single, good quality ball mill circuit survey, the plant metallurgist, process consultant, or circuit designer can generate a Streamline™ model and quickly find the practical limit of CSE attainable for a given circuit along Many kinds of these plants have been developed Perhaps the most common ones are based on recirculation through a ball mill (Beckett, 1999), which employs the relative motion of loose elements (balls) to generate a grinding action They are typically vertical or horizontal cylinders, equipped with a rotating shaft with arms, filled to as much as 90% of the available volume with grinding media Optimization of processing parameters of a ball mill During the grinding process, coarser material (size class 1) break to finer material (size class 2) and (size class 3) which are termed the daughter products, as shown in Fig 1A chemical reaction on the other hand can consist of say reactant ‘A’ forming intermediate product ‘B’ then proceeding to final product ‘C’ or a competing reactant ‘A’ to final product ‘D’ can also Effect of ball and feed particle size distribution on the
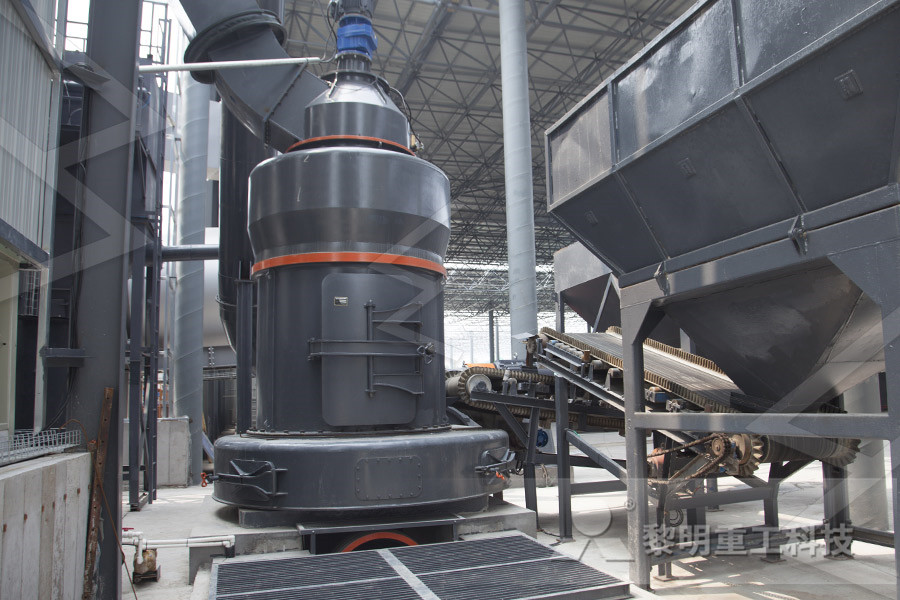
Lihir Facts Processing Tripod
The ball mill cyclone overflow can be split to divert up to 120tph at 30% solids through the pilot Flotation circuit Design flotation time is 14 minutes and concentrate production is 4050 dtph Feed can also be obtained from the Pre oxidation storage tanks8322 Ball mills The ball mill is a tumbling mill that uses steel balls as the grinding media The length of the cylindrical shell is usually 1–15 times the shell diameter ( Figure 811) The feed can be dry, with less than 3% moisture to minimize ball coating, or slurry containing 20–40% water by weightBall Mills an overview ScienceDirect TopicsVideo about Ball mill at a cement plant Ball mill in the mining industry Video of process, cement, manufacturing Ball mill in the mining industry Ball mill at a cement
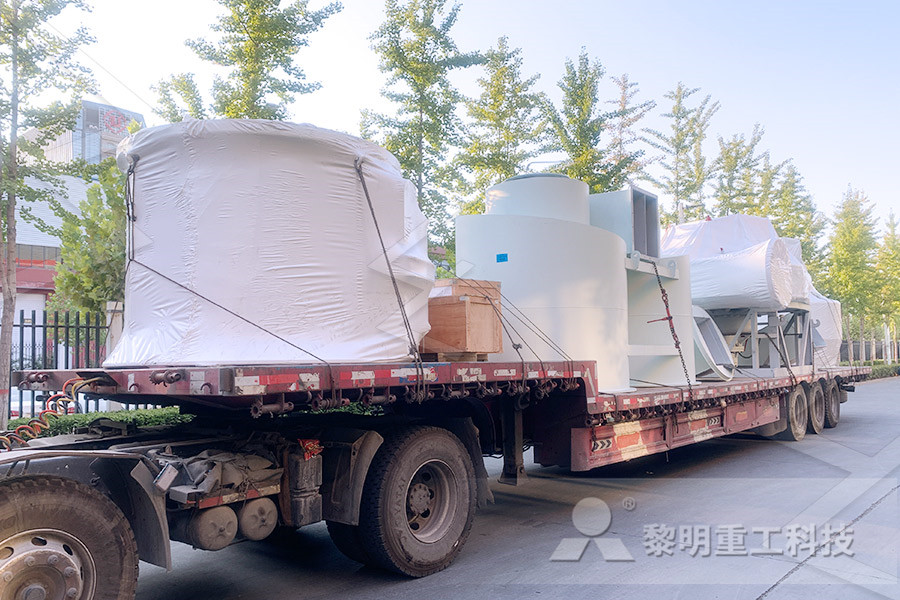
Lead: Battery Manufacturing eTool Oxide and Grid
Lead oxide, which is used to create the paste used on the battery plates, is either produced by the Ball Mill Process or the BartonLike ProcessIt may also be purchased from an oxide producer (see receiving) The major source of lead exposure in the oxide production process The layout of the plant and a ball mill image are shown in Fig 1, Fig 2 Download : Download fullsize image; Fig 1 Layout of the SOTUMILL/130 plant (Packint, Milano, Italy) used to perform experiments The line is composed of a powder feeder (1), a ball mill (2) a recycling pump (3) and a tank to store the refined chocolate (4)Optimization of processing parameters of a ball mill 2) Ball milling – a ball mill with a diameter of 244 meters, inside new liners, grinding wet in open circuit When the grinding conditions differ from these specified conditions, efficiency factors (Rowland and Kjos, 1978) have to be used in conjunction How to Size a Ball Mill Design Calculator Formula
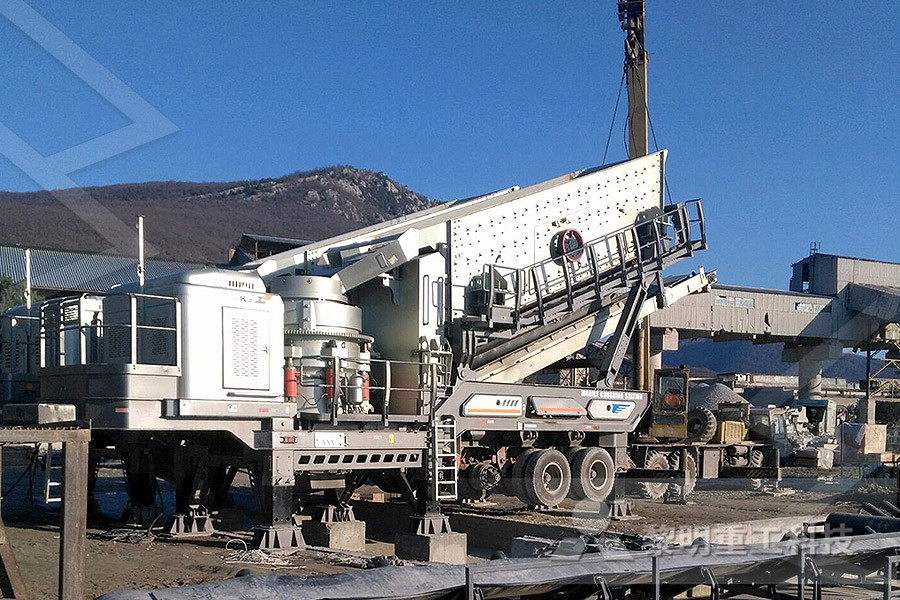
Optimizing Performance of SABC Comminution Circuit of
the SAG mill and ball mill was 8658 kW, which caused partial overgrinding From experience in processing plants outside of China, the power rating of the ball mill should be higher than that of the SAG mill [5] The pebble crusher had an overpowered configuration The installed power draw of 630 kW This resulted in a very complex process plant design The final design had (inside shell) x 52long (effective grinding length) overflow ball mill that will be fitted with a 900kW motor The ball mill will be in closed circuit with 250 mm diameter cyclones The ball mill will grind the ore to 80% passing 75µmAPPENDIX 2: CAPITAL AND OPERATING COST ESTIMATE further reduced in size Water is added to the ball mill, in which a slurry that usually contains from about 20 to 55 percent solids is produced (Singh, 2010; International Mining, 2011) (see fig 2) The mill operates in a closed circuit with screens that size the Estimated Water Requirements for the Conventional
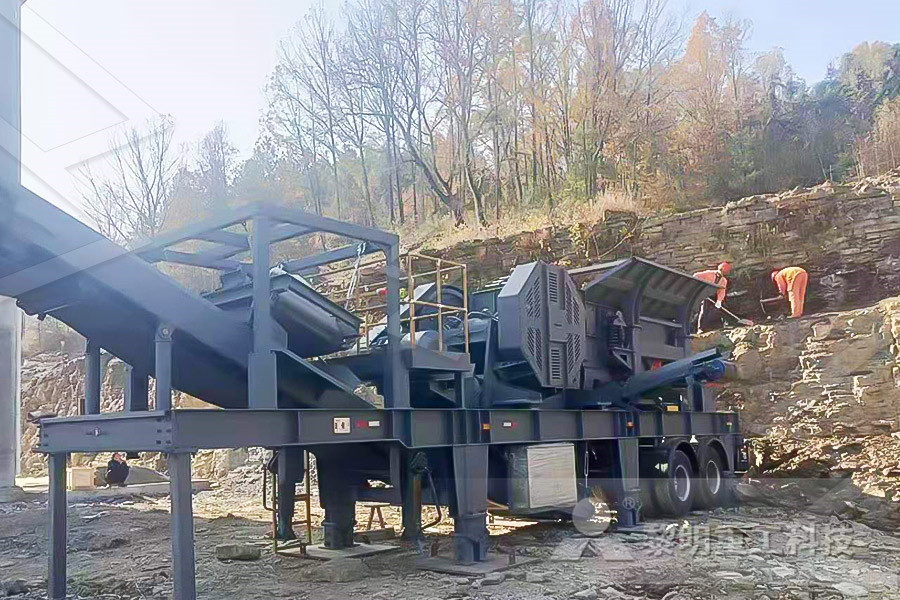
SAFETY GUIDELINES FOR IRON STEEL SECTOR
221 Pretreatment process of Iron Ore Fines In the pretreatment process, iron ore fines are ground into finer size, suitable for green ball formation Dry or wet grinding process is adopted for grinding the iron ore fines In dry grinding process, equipment ie drier, ball mill,Process Control General Description Lihir processing plant is designed to process 36 Mtpa of ore containing 72% sulphide sulphur at a gold grade of up to 13 g/t and a plant availability of 86% The instantaneous design feed rate is 375 t/h of ore containing 27 t of sulphide sulphur There is a legal obligation under the mining permit to Lihir Facts Processing TripodBall Mill for Cement Grinding Process Cement ball mill structure when ball mill is working, raw material enters the mill cylinder through the hollow shaft of the feed the inside of the cylinder is filled with grinding media of various diameters steel balls, steel segments, etc when the cylinder rotates around the horizontal axis at a certain speed, under the action of centrifugal force and inside process of ball mill used for gringing
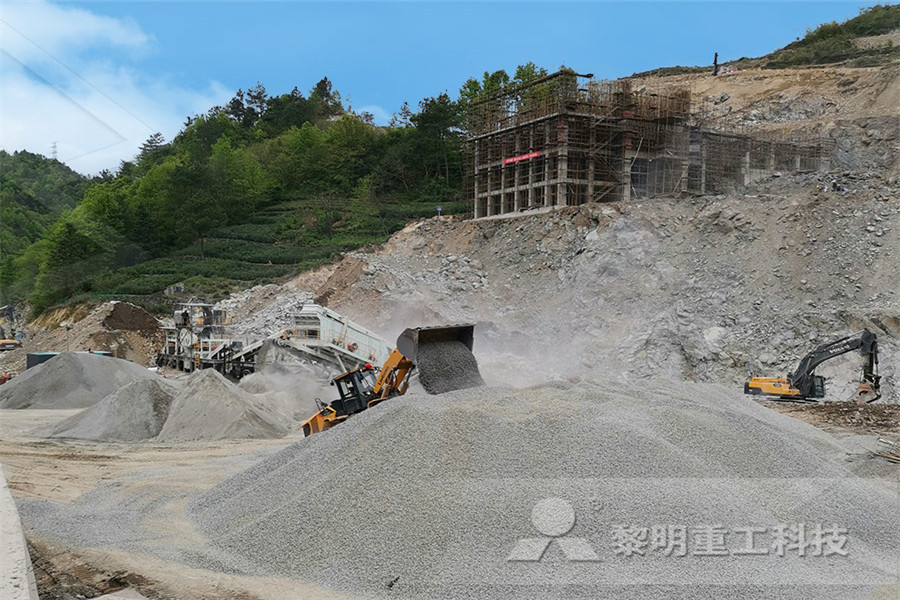
Ball Mill: Operating principles, components, Uses
A ball mill also known as pebble mill or tumbling mill is a milling machine that consists of a hallow cylinder containing balls; mounted on a metallic frame such that it can be rotated along its longitudinal axis The balls which could be of different diameter occupy 30 – 50 % of the mill volume and its size depends on the feed and mill Ball mill Application: It is widely used in cement, silicate products, new building materials, refractories, fertilizers, black and nonferrous metal beneficiation and glass and ceramics industries Material: Iron ore, slag, copper ore, silver ore, galena and other materials The ball mill Ball millHenan Hongji Mine Machinery Co, Ltd This resulted in a very complex process plant design The final design had (inside shell) x 52long (effective grinding length) overflow ball mill that will be fitted with a 900kW motor The ball mill will be in closed circuit with 250 mm diameter cyclones The ball mill will grind the ore to 80% passing 75µmAPPENDIX 2: CAPITAL AND OPERATING COST ESTIMATE
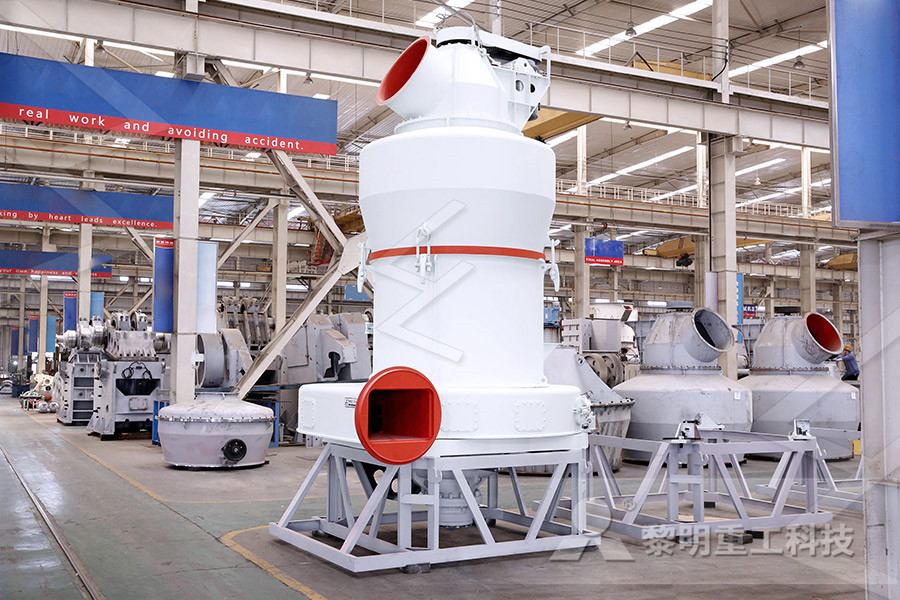
PT Freeport Indonesia
4 Ball Mill 24 ft WEMCO 36x4500 ft3 sel flotasi Process Overview • Ore Processing Plant Area, located in area MP74 The mill produces copper and gold concentrate from mined ore through a process to separate valuable minerals from the impurities covering them The main steps in the process are crushing, grinding, flotation, and dewatering The power ingesting of a grinding process is 5060% in the cement production power consumption The Vertical Roller Mill (VRM) reduces the power consumption for cement grinding approximately 3040% associated with other grinding mills The process variables in cement grinding process using VRM are strongly nonlinear and having large timePROCESS CONTROL FOR CEMENT GRINDING IN AND PLANT BASED ON BS 1553: PART 1: 1977 Scope This part of BS 1553 specifies graphical symbols for use in flow and piping diagrams for process plant A1 Symbols (or elements of Symbols) for Use in Conjunction with Other Symbols Mechanical linkage ball mill Mixing (basic symbol) Kneader Ribbon blender Double cone blenderA GRAPHICAL SYMBOLS FOR PIPING SYSTEMS AND PLANT
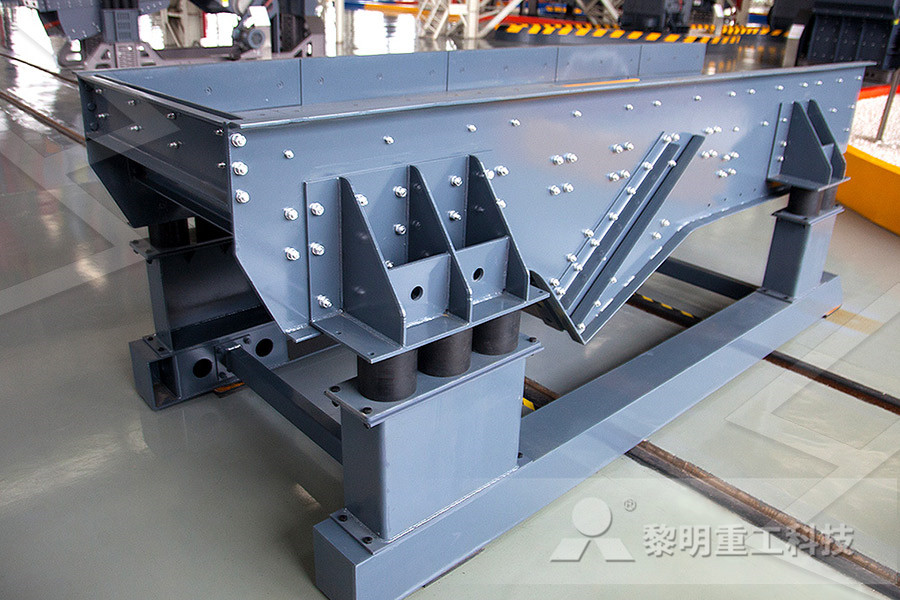
Back to Basics Hammer Milling and Jet Milling
process must be illustrated clearly in a yearly, monthly, daily, and hourly rate The capacity not only determines the mill equipment size, but also dictates how to operate the mill, whether continuous or batch operation is required, and whether the process can be performed inhouse or if a tolling service is a better optiongraphical, functional interface Metris OPP (Optimization of Process Performance) combines Big Data analytical capabilities with our highly skilled process and equipment experts to perform a truly unique service With Metris OPP, the vast amount of data generated by plant sensors and conINSIDE: Process and plant optimization Mill Lubrication System 1 OBJECTIVES: To identify the definition and importance of a hydraulic lubrication system To be familiarized with the lubricant and equipment used in the system To understand the process and various design of Mill lubrication systemMill Lubrication System SlideShare