Case
significant size reduction after ball milling
2021-02-27T11:02:58+00:00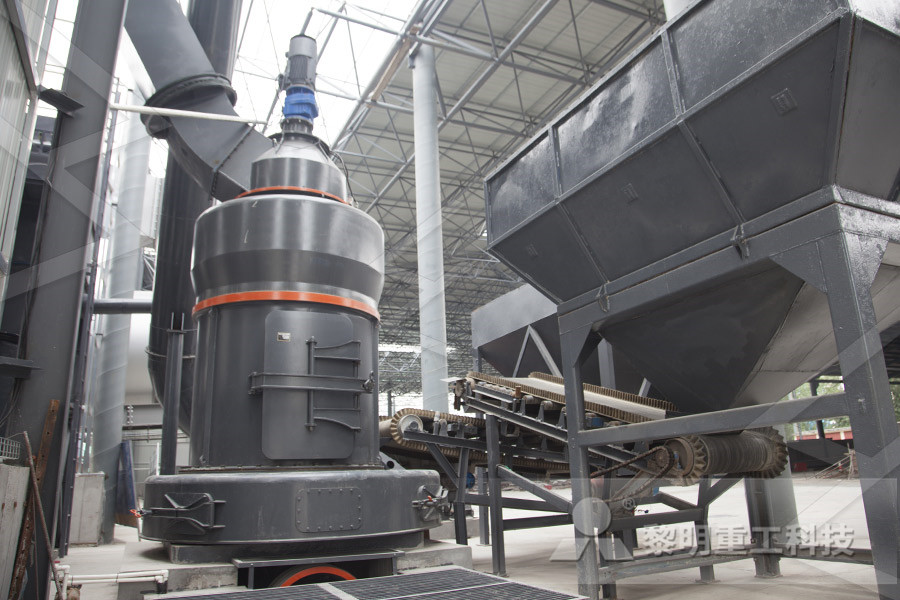
significant size reduction after ball milling
The different type of ball milling can be used for synthesis of nanomaterials in which balls impact upon the powder charge 1 There was a significant reduction in Al 2 O 3 grain size after 24h milling up to 27nm and approached the alloy grain Chat Online; Ball Mill LoadingDry MillingPaul O Abbe The high energy impact between the jar of specialized geometry and the balls causes significant reduction in the particle size This paper aims to develop a process to use high energy ball milling to produce HY zeolites nanoparticlesInsight into ball milling for size reduction and The cumulative PSD also shows a significant size reduction between 60 min and 600 min of milling but a less significant difference between 600 and 1200 min Interestingly the PSD after 60 min milling showed larger particles than in the AR sample This is presumably due to adhesion of fine particles with high surface energy on the surfaces of larger agglomeratesEffect of mill type on the size reduction and phase
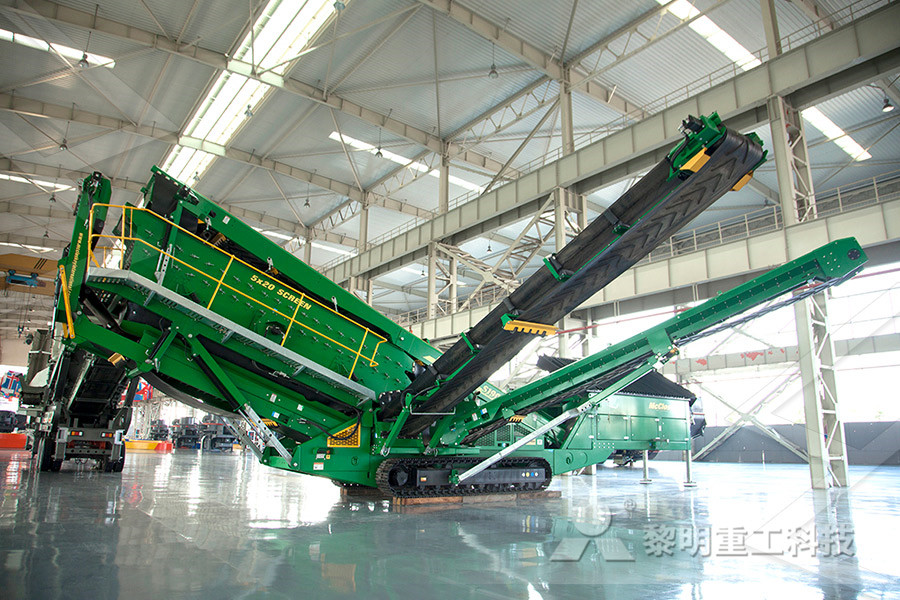
Size Reduction an overview ScienceDirect Topics
The size of the milling media (typically 20:1 for ball:powder diameter) also influences size, morphology and microstructure of the powder To produce fine powders, it is recommended to mill in several steps while reducing successively the milling media size, as one milling step usually induces a particle size reduction of about factor 10 It may be observed that wet ball milling led to a significant reduction in the median particle size of the original zeolite HY sample This size, which was initially slightly above 6 μm, could be decreased below 1 μm after 8 h of wet ball milling in all the three sets of experiments performedWet ball milling of zeolite HY ScienceDirectBall milling and ultrasonication were used to reduce the particle size and distribution During ball milling the weight (grams) ratio of ballstoclay particles was 100:25 and the milling operation was run for 24 hours The effect of different types of balls on particle size reduction and narrowing particle size distribution was studied The Ball Milling an overview ScienceDirect Topics
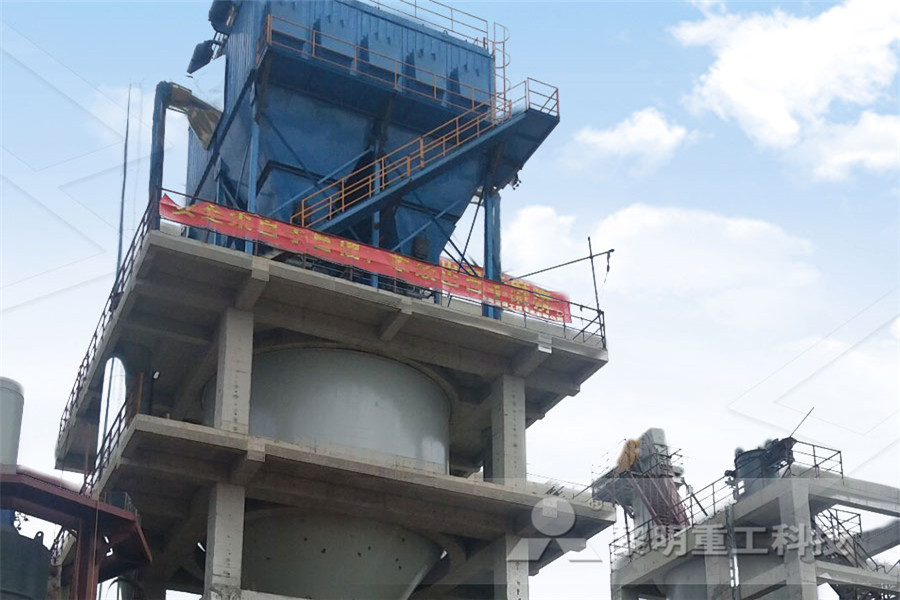
Exploring the relationship between solventassisted
Conversely, ball milling in acetonitrile with a small amount of surfactant (to improve dispersion) successfully reduced the particle size to ~220 nm (Dv50) without significant lithium loss, and subsequent sintering experiments showed that using a smaller particle size decreased the minimum sintering temperature by 100 °C When the ball milling speed increases from 200 to 400 rpm, the average particle size of the sample decreases significantly by 321 nm, 759% compared with the average particle size at 200 rpm However, when the ball milling speed increases from 400 r/min to Effect of ball milling process on the photocatalytic The effects of key process parameters (rpm, bead size and total drug content) on mean particle size were determined after 4 h of milling In addition to these results, a basic time course study was carried out for each milling run with the intent of determining the effects of different process parameters on the rates of particle size reduction Optimization of formulation and process parameters
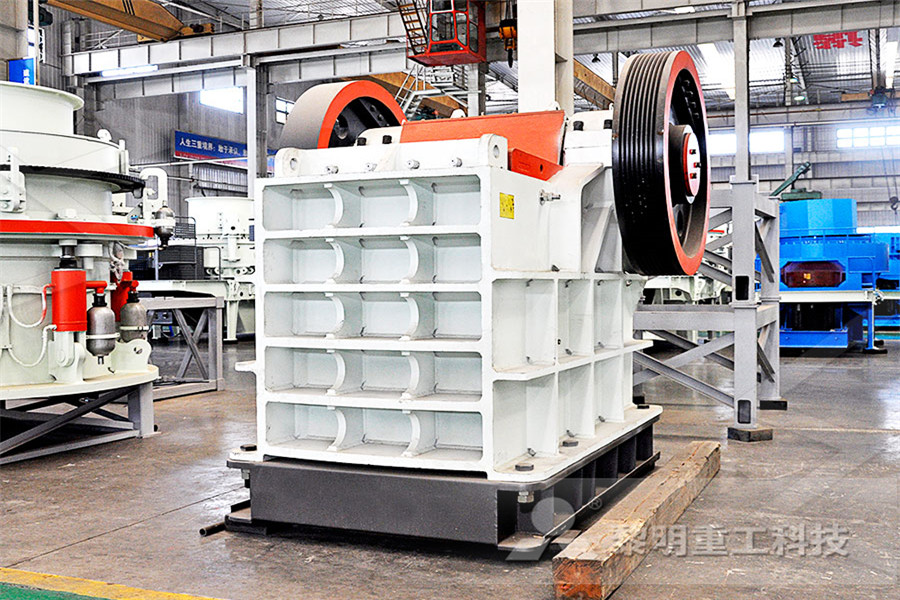
Lab 7 The effect of ball milling on particle size of
CALCULATION CONCLUSIONS Make conclusions based on the following questions: 1 From the histogram, is the distribution of particle size uniform after ball milling 2 How do you measure the average particle size of samples 3 From the graph, is there any significant size reduction after ball milling Whereas, in 350 RPM significant particle size reduction appeared after 10 hours of milling in Al5at%V and Al10at%V (Fig 4a and 6a, respectively) and further milling lead to coarsening of the particles (Fig 4b and 6b) For both the milling speeds, the average particle sizes after a given milling time reduced with the increase in V contentThe Effect of Milling Time and Speed on Solid effect of ball milling and solvent displacement method on size reduction of Celecoxib particles Celecoxib is a poorly water soluble cyclooxygenase 2 inhibitor which has a wide range of therapeutic applicability Methods:Keywords: Microparticles were developed via solvent displacement method followed by planetary ball bination of Solvent Displacement and Wet Ball
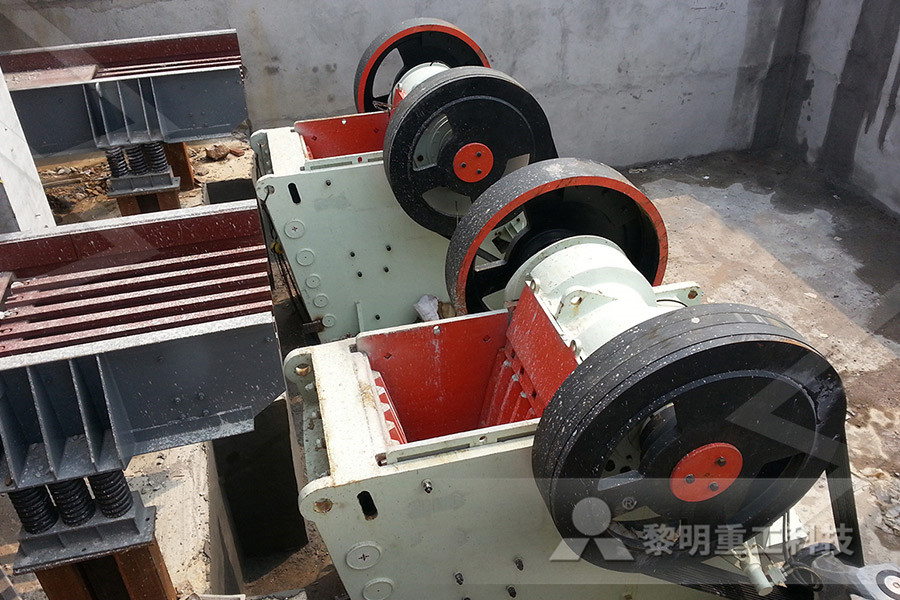
Ultrasonic Milling of Thermoelectrical NanoPowders
Ultrasonic milling for only 4h of Bi 2 Te 3alloy already yielded in a substantial amount of nanoparticles with sizes between 150 and 400 nmBesides the size reduction to the nano range, sonication also resulted in a change of surface morphology The SEM images in the figure below b, c, and d display that the sharp edges of the particles before ultrasonic milling The dry milling dramatically reduced the size of the chitin particles from a median particle size of 1428 µm to a median particle size of 138 µm, a roughly tenfold size reduction after the milling (Fig 1a) The wet ball milling reduced the size of the chitin particles to a median size of 455 µm under the neutral condition (pH7/WBM) and The influence of prefibrillation via planetary ball This article analyzes the influence of mechanical ball milling parameters on processed aluminum bronze chips in order to increase the efficiency of this process in terms of particles' size reduction Also evaluated is the addition of vanadium carbide (VC) in this response, along with its microstructure and magnetic properties The experiments have been carried out in accordance with Influence of ball milling parameters on microstructure
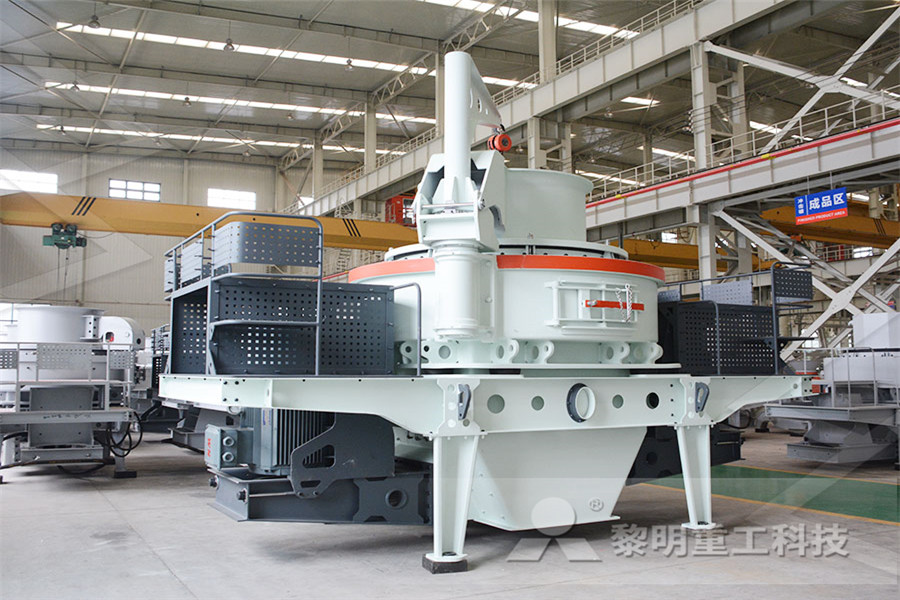
Metallothermic reduction of zinc sulfide induced by
Stoichiometric mixtures of ZnS + Al and ZnS + Mg were milled for different times in a planetary ball mill The XRD traces of the asmilled samples showed the presence of zinc, MgZn2, and MgS after 30min milling in the ZnS–Mg system The traces of MgZn2 disappeared after 1h milling and the reduction reaction seemed to have been completed after 5h millingAfter just 10 s of milling, the average particle size was reduced from D n ≈ 30 µm for the asreceived powder to a level of approx 10 µm after highenergy milling The obtained mean particle size values indicate that this material remained at a similar level of refinement in the size range from 89–101 µm throughout the milling process Materials Free FullText New Aspects of MgH2 Abstract CdS/TiO 2 composite photocatalysts were made by the method of secondary ball milling at different ball milling speeds, milling time, and material ratios After the secondary ball milling process, parts of the samples were calcined at high temperatures Xray diffraction (XRD) and UVVis diffuse reflectance spectroscopy (DRS) were used to observe the powder particle size, structural Effect of ball milling process on the photocatalytic
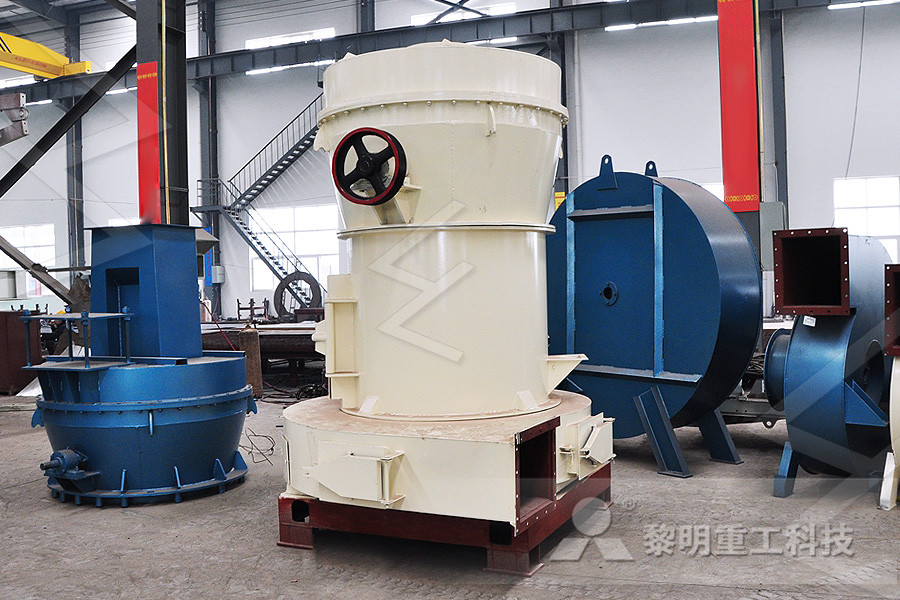
II PREPARATION OF POWDERS Milling, grinding and size
(Milling, grinding and size reduction) Fine particles possess high surface energy, which favors physicochemical reactions between the solid and surrounding medium After milling the fesh surface acquired hydrophilic properties and adsorbed relatively large quantities of water vaporof coarse sugar for the 5 minutes shows a significant size reduction after ball from FST 359 at Universiti Teknologi Maraof coarse sugar for the 5 minutes shows a significant effect of ball milling and solvent displacement method on size reduction of Celecoxib particles Celecoxib is a poorly water soluble cyclooxygenase 2 inhibitor which has a wide range of therapeutic applicability Methods:Keywords: Microparticles were developed via solvent displacement method followed by planetary ball bination of Solvent Displacement and Wet Ball

Micronization of a soft material: airjet and microball
Ball milling produced particles less than 10 microm after 15 min Although airjet milling proved capable of particle size reduction of the relatively soft material Pluronic F68, limitations to the lower size range achievable were observed The reduction of particle size by the ball milling process is a function of milling time, milling energy For all experiments under all conditions, the particle size reductions achieved are in the range of 100 nanometre This result shows that the reduction in particle size by ball milling is limited by ball size and componentsBehavior of CuWCTi Metal Composite After using Definition, objectives of size reduction and size separation, factors affecting size reduction, laws governing energy and power requirements of mills including ball mill, hammer mill, fluid energy mill etc, sieve analysis, standards of sieves, size separation equipment shaking and vibrating screens, gyratory screens, cyclone separator, air separator, bag filters, cottrell precipitator SIZE REDUCTION AND SIZE SEPARATION
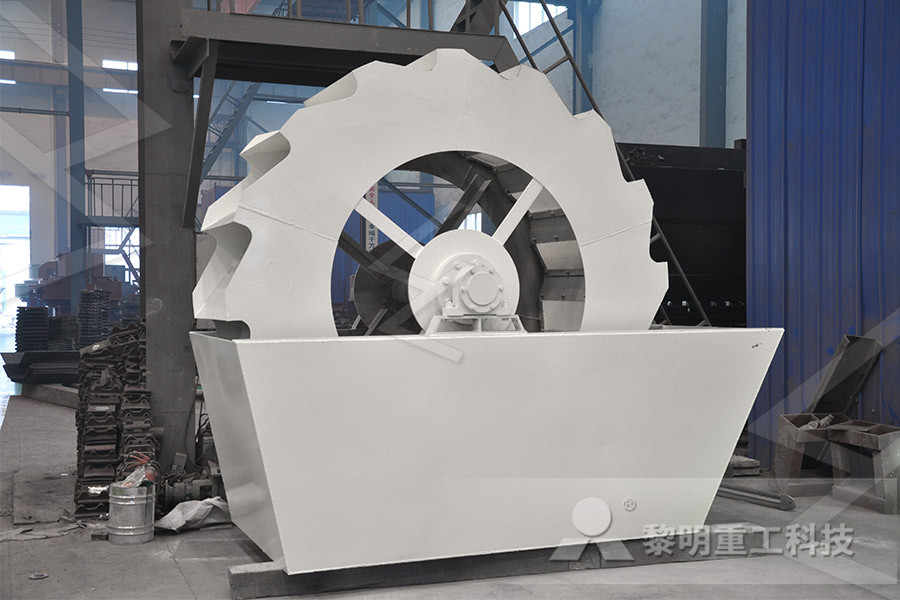
Effects of Ball Milling Processes on the Microstructure
After 1h of ball milling, the compact rigid structure of the cellulose crystallites transformed into a loosened needlelike structure exhibiting an intuitive reduction in size (Figure 1 b) After 2 h of ball milling, the microcrystalline structure was crushed into small fragment, with a more pronounced decrease in length than in width Last but not least, there is significant size reduction of coarse sugar after the milling was occurred This is due to the graph plotted at the aperture size 1000 mm, before the coarse sugar was milled, the undersize cumulative fractions was 8263 meanwhile after the milling LR 7 FST 559docx FST559 UNIT OPERATIONS Synthesis of nanomaterials by a simple, low cost and in high yield has been a great challenge since the very early development of nanoscience Various bottom and top down approaches have been developed so far, for the commercial production of nanomaterials Among all top down approaches, high energy ball millingMechanical Milling: a Top Down Approach for the