Case
requirements of gold leaching process
2023-12-12T16:12:40+00:00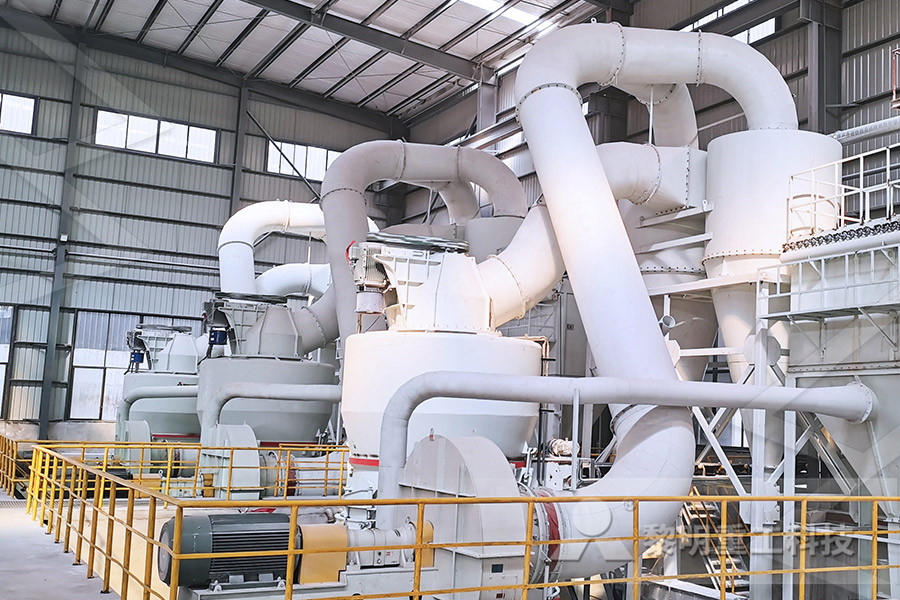
Estimated Water Requirements for Gold HeapLeach Operations
The HeapLeach Process Briefly stated, gold heap leaching is a hydrometallurgical process designed to treat amenable lowgrade gold ores that contain roughly 05 gram per metric ton (g/t) gold to 15 g/t gold (Marsden and House, 2006; Wong Wai Leong and Mujumdar, 2010) The ore is stacked by various types of equipmentLeaching, often gold, is the process of extracting a soluble constituent from a solid by means of a solvent In extractive metallurgy, of gold, it is the process of dissolving a certain mineral (or minerals) from an ore or a concentrate, or dissolving certain constituents from materials such as a calcines, mattes, scrap alloys, anodic slimes, etc, to achieve either one or two purposes Gold Metallurgy and Leaching Processspent goldbearing alloys coming from the electronic industry, jewelry, and dentistry sectors2 All the hydrometallurgical gold extraction routes utilize a leaching step to produce a goldbearing solution as an intermediate product while the recycling of secondary gold from electronic and precious metal scrap isA Method for Leaching or Dissolving Gold from Ores or Apr 25, 2018 In the case of gold recovery, heap leaching generally requires 60 to 90 days to leach the ore, compared to the 24 hours required by a conventional agitated leach process Gold recovery is also usually only 70% compared with 90% recovery in an agitated leach plantHeap leaching a stack of gold MiningFeedsThiosulphate leaching is a process that removes gold from gold bearing ores without the use of cyanide Although not as aggressive a leaching agent as cyanide, thiosulphate offers several technological advantages including its lower toxicity and greater efficiency with gold deposits associated with pregrobbing ores The thiosulphate leaching THIOSULPHATE LEACHING – AN ALTERNATIVE TO
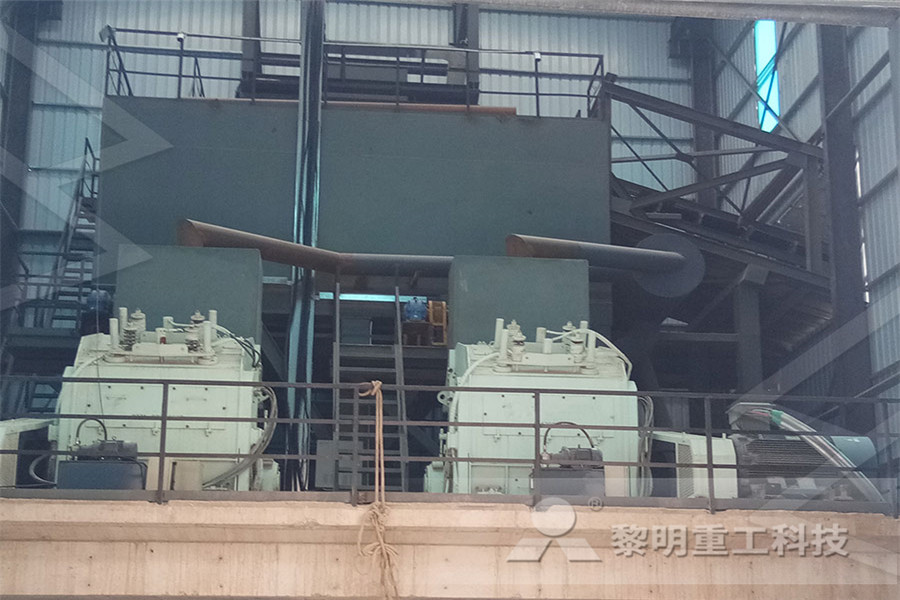
Gold Extraction an overview ScienceDirect Topics
Jeffrey et al (2008a,b) observed that increasing the pH value from 85 to 105 increased the gold leaching efficiency from 7% to 70% from a pressureleach residue of a refractory gold ore after 1 h in 50 mmol/L (NH 4) 2 S 2 O 3 and 05–2 mmol/L CuSO 4from the dissociation of the complex is used to leach gold from the ore The stepwise dissociation of cyanide from coppercyanide complexes can also be used to leach gold from a variety of oxide and sulphide ores The copper cyanide's fourth ligand readily dissociates at low cyanide concentrations for use in gold leachingThe leaching and adsorption behaviour of gold oresOutotec's cyanide leaching plants are available as gold adsorption directly from the process slurry in carboninleach (CIL) and carboninpulp (CIP) processes In addition, dissolved gold can be recovered from the solution after solidliquid separation by MerrillCrowe and carbonincolumn operationsGold Cyanide Leaching Process Outotec5 Leaching time Gold cyanide leaching is a relatively slow process, the leaching time is over 24 hours generally, and the gold leaching rate is improved with the extension of leaching time, but the gold leaching speed is reduced corresponding, and finally, the gold leaching rate tends to a limit valueSix Factors Affecting Gold Leaching in Cyanide Leaching Thiosulfate leaching offers a number of benefits related to gold recovery yields and environmental concerns: Thiosulfate leaching of gold ores has great potential to reduce the impact on the environment Unlike cyanide, which is highly toxic, the chemicals used in the thiosulfate leaching process are benignThiosulphate Leaching SGS
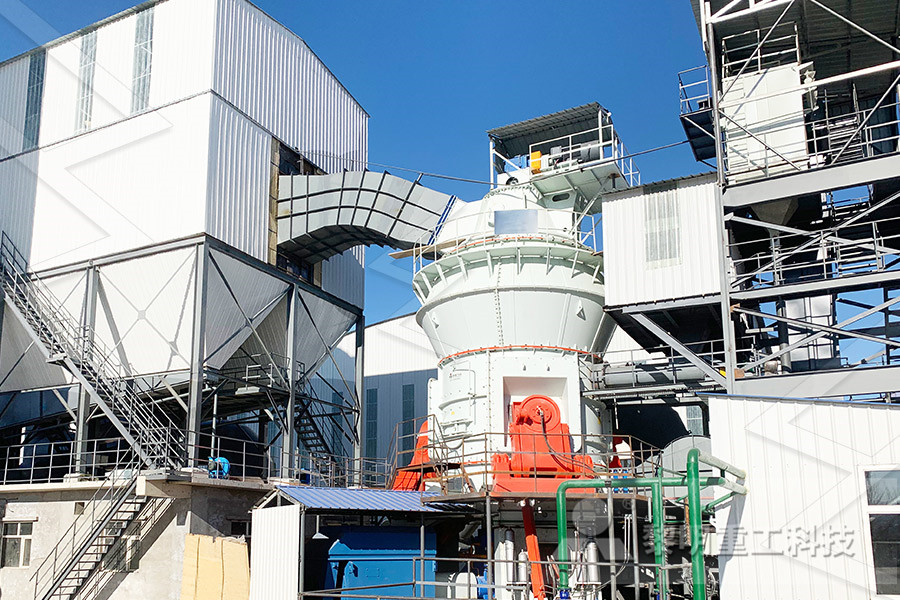
GOLD AND SILVER
Cyanidation leaching is the primary means of recovery of fine gold and silver In this process, solutions of sodium or potassium cyanide are brought into contact with an ore which may or may not have required extensive preparation prior to leaching Gold and silver are dissolved by cyanide in solutions of high pH in the presence of oxygenLeaching dissolves the gold out of the ore using a chemical solvent The most common solvent is cyanide, which must be combined with oxygen in a process known as carboninpulp As the cyanide and oxygen react chemically, gold in the pulp dissolvesExtracting Gold HowStuffWorksLeaching is the only process to extract metallic content from the lowgrade ores Among leaching methods — Heap leaching is most economical; major advantage of Carbon in Pulp is not the reduction in the use of zinc dust but rather the impact on the dewatering requirements Using carbon allows the gold to be recovered on coarse pellets (16 AMIT 145: Lesson 7 Leaching – Mining Mill Operator TrainingNov 29, 2019 A simple flowchart for a gold heap leaching process(Source: modified from Donald, IB Estimated Water Requirements for Gold HeapLeach Operations (ver11,11 December2012): US Geological Survey OpenFile Report 2012–1085 pp 1–17Heap Leaching: Is it something that could be an Introduction of VatLeachingVat leaching has been around since Roman times, but had become viable in 1896, when cyanide leaching began in earnest with the MerrillCrowe ProcessIn an article in the Engineering and Mining Journal in December 1999, Lou Cope described the first vat leaching at Homes take in 1901, which later improved the process in 1906 by adding a desliming circuit(DOC) VAT LEACHING AND ELUTION PLANT GOLD
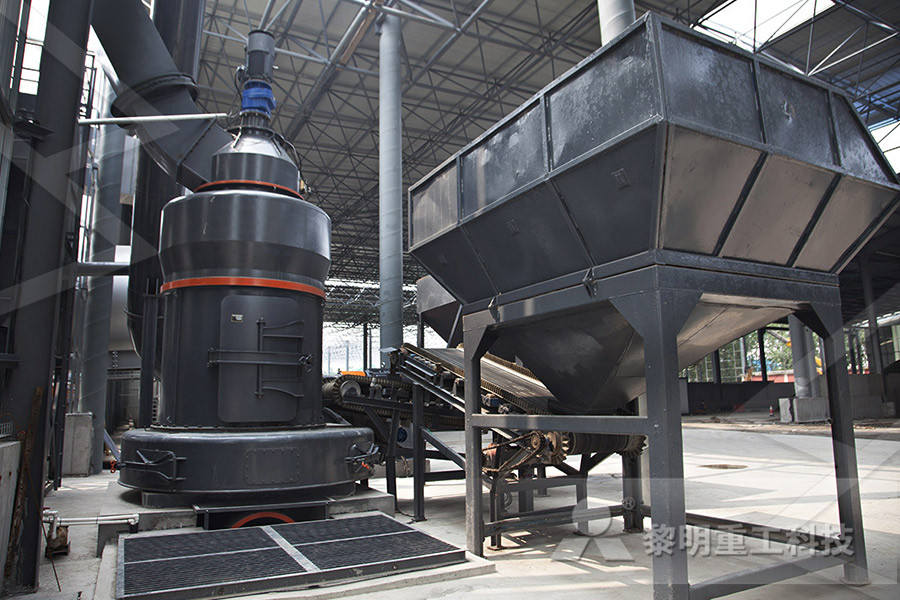
MET63 leaching technology Met 63
Toll treatment of gold, copper and nickel runofmine, or tailings Capital requirements lower than conventional leaching technologies; Higher metal recoveries compared to heapleach operations; at University of Pretoria is ongoing on gold ores to generate a data base for current and future hydrometallurgical process plant designThe applicability of the optimized iodide leaching process for the extraction of gold from the leach residue obtained after HPOL were examined at different pulp densities ranging from 50 g/t to NonCyanide Leaching Processes in Gold Hydrometallurgy and The process design of gold leaching and carboninpulp circuits contaminants These are removed by thermal regeneration of the eluted carbon, typically in a rotary kiln at temperatures of 650–750°C Regeneration is carried out in a steam atmosphere to minimize carbon degradation due to oxidationThe process design of gold leaching and carboninpulp The gold mine pool leaching process has strict requirements on the dosage of cyanide solution; too much is of a waste and too little can't guarantee the leaching effect When using CNFREE ecofriendly gold leaching reagent, the requirements can be appropriately relaxed in terms of dosage,and the same leaching effect of cyanide can be obtained Gold CIP, CIL System, Heap Leaching, Cyanidation Process Cyanide heap leaching is a process for recovering gold and silver by trickling cyanide solutions through lowgrade ore that has been stacked on openair pads (Fig 1) Cyanide heapleach methods are viewed by industry as offering a lowcost means of producing precious metals The natural oxidizing conditionsWASHINGTON STATE DEPARTMENTOF Natural Resources
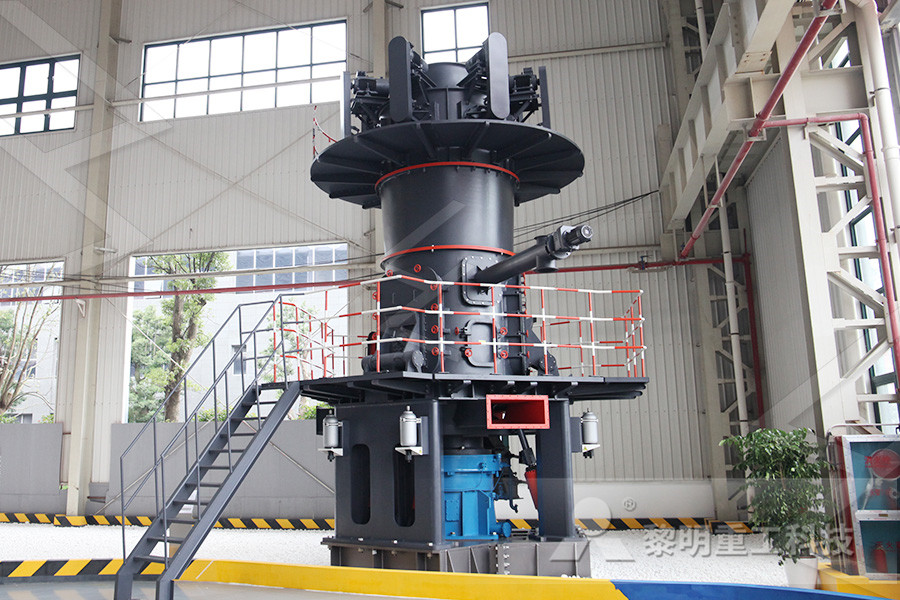
The process design of gold leaching and carboninpulp
The process design of gold leaching and carboninpulp circuits contaminants These are removed by thermal regeneration of the eluted carbon, typically in a rotary kiln at temperatures of 650–750°C Regeneration is carried out in a steam atmosphere to minimize carbon degradation due to oxidationThe process: The ore is ground and crushed to make a slurry The treated gold then has sodium cyanide added to it and the following reaction: Au + 2 CN→ Au(CN) 2In this form the gold is now soluble This process is known as leaching This reaction is normally carried out at a pH of 1011 as this prevents cyanide ion being converted toExtraction of gold using cyanide5 Leaching time Gold cyanide leaching is a relatively slow process, the leaching time is over 24 hours generally, and the gold leaching rate is improved with the extension of leaching time, but the gold leaching speed is reduced corresponding, and finally, the gold leaching rate tends to a limit valueSix Factors Affecting Gold Leaching in Cyanide Leaching Cyanidation leaching is the primary means of recovery of fine gold and silver In this process, solutions of sodium or potassium cyanide are brought into contact with an ore which may or may not have required extensive preparation prior to leaching Gold and silver are dissolved by cyanide in solutions of high pH in the presence of oxygenGOLD AND SILVERThe cyanide solution strength is also important in leaching gold, with the typical range of solution being in the 002% 005% NaCN The gold particle size has a tremendous effect on the time required for dissolution in a cyanide solution Generally, the finer the gold, the quicker it will dissolveCyanide Leaching Of Gold Mine
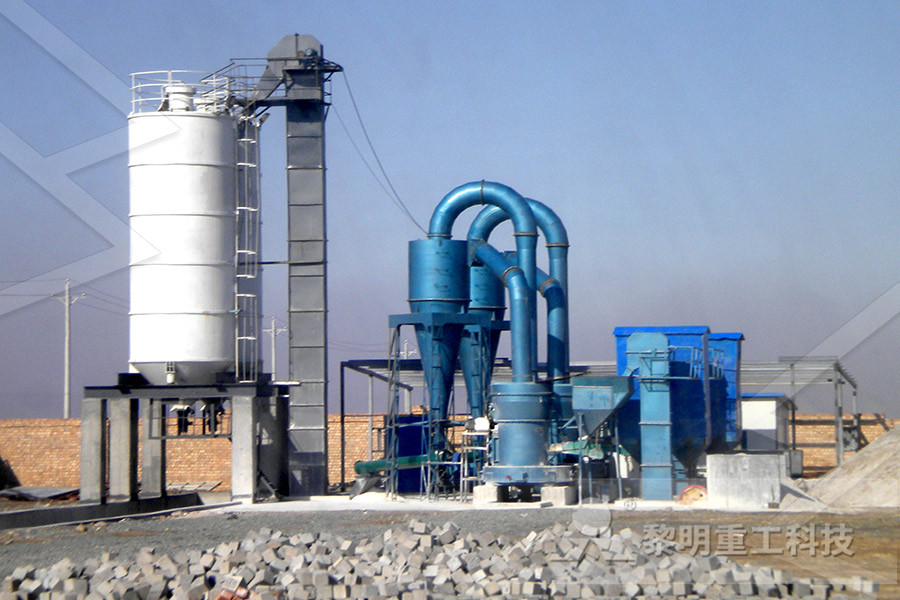
(DOC) VAT LEACHING AND ELUTION PLANT GOLD
Introduction of VatLeachingVat leaching has been around since Roman times, but had become viable in 1896, when cyanide leaching began in earnest with the MerrillCrowe ProcessIn an article in the Engineering and Mining Journal in December 1999, Lou Cope described the first vat leaching at Homes take in 1901, which later improved the process in 1906 by adding a desliming circuitLeaching is the only process to extract metallic content from the lowgrade ores Among leaching methods — Heap leaching is most economical; major advantage of Carbon in Pulp is not the reduction in the use of zinc dust but rather the impact on the dewatering requirements Using carbon allows the gold to be recovered on coarse pellets (16 AMIT 145: Lesson 7 Leaching – Mining Mill Operator TrainingThe applicability of the optimized iodide leaching process for the extraction of gold from the leach residue obtained after HPOL were examined at different pulp densities ranging from 50 g/t to NonCyanide Leaching Processes in Gold Hydrometallurgy and • Heap Leaching • Heap leaching was introduced in the 1970’s as a means to drastically reduce gold recovery costs This process has literally made many mines by taking low grade geological resources and transforming them to the proven ore category Ore grades as low as 001 oz Au per ton have been economically processed by heap leaching 8Bioleaching gold recovery SlideShareMobile leaching solutions, combining leaching, solidliquid separation, and washing Capable of leaching gold and base metals (ore dependent) No milling required – MET63 leaching technology Met 63

Leaching Adsorption Resource Book
After the leaching process is complete, the soluble gold must be concentrated and separated from the process slurry The method of recovery of gold from the process slurry is by carbon adsorption Adsorption is a term used to describe the attraction of a mineral Cyanidation, or the metallurgical process of extracting gold from ore with cyanide leaching agents, has long been a primary method of gold beneficiationWidely used throughout the world, one incredible material helps to make gold recovery from a cyanide solution possible; with its ultraporous structure, activated carbon is a powerful adsorbent used throughout a number of industries to Activated Carbon in Gold Cyanidation(1) For the buildings to which the sand gold equipment is attached, the strength of the anchor points should meet the planning requirements of the sand gold equipment The arrangement method, mutual spacing and attachment interval of the attachment rod system shall be implemented in accordance with the rules of the factory operation manualThe strength requirements of sand gold equipment on the Aug 20, 2015 Heap Leaching of Gold In 2014 about 150 major goldsilver mines worldwide utilized HL technology and recovered about 15 million troy ounces of gold, roughly 17% of global gold Heap Leach: Mining's breakthrough technology